氮化是鋼件表面改性強(qiáng)化處理的工藝方法之一。當(dāng)代輝光離子氮化、雙程氮化、三段氮化和預(yù)氧化雙程氮化及催滲氮化等方法發(fā)展了傳統(tǒng)氮化工藝,使氮化質(zhì)量達(dá)到了新水平。
將氮化介質(zhì)氨氣通入氮化爐中,加熱至500~6000℃發(fā)生熱分解:2NH3≒2[N]+3H2。分解活性[N]原子被鋼件表面吸收,并向金屬內(nèi)部擴(kuò)散,首先溶解在α-Fe中形成固溶體,飽和后逐漸形成氮化物層。滲氮層具有高硬度、高耐磨、高抗疲勞強(qiáng)度和較高抗蝕性及熱處理畸變小等特點(diǎn),廣泛應(yīng)用于模具制造業(yè)。模具經(jīng)氮化處理后,可成倍、甚至數(shù)倍提高模具使用壽命。但在實(shí)際生產(chǎn)中,因種種原因會產(chǎn)生各種各樣的氮化缺陷,本文分析了其產(chǎn)生原因,并提出了相應(yīng)的消除措施。
傳統(tǒng)的合金鋼料中之鋁、鉻、釩及鉬元素對滲氮甚有幫助。這些元素在滲氮溫度中,與初生態(tài)的氮原子接觸時,就生成安定的氮化物。尤其是鉬元素,不僅作為生成氮化物元素,亦作為降低在滲氮溫度時所發(fā)生的脆性。其他合金鋼中的元素,如鎳、銅、硅、錳等,對滲氮特性并無多大的幫助。一般而言,如果鋼料中含有一種或多種的氮化物生成元素,氮化后的效果比較良好。其中鋁是最強(qiáng)的氮化物元素,含有0.85~1.5%鋁的滲氮結(jié)果最佳。在含鉻的鉻鋼而言,如果有足夠的含量,亦可得到很好的效果。
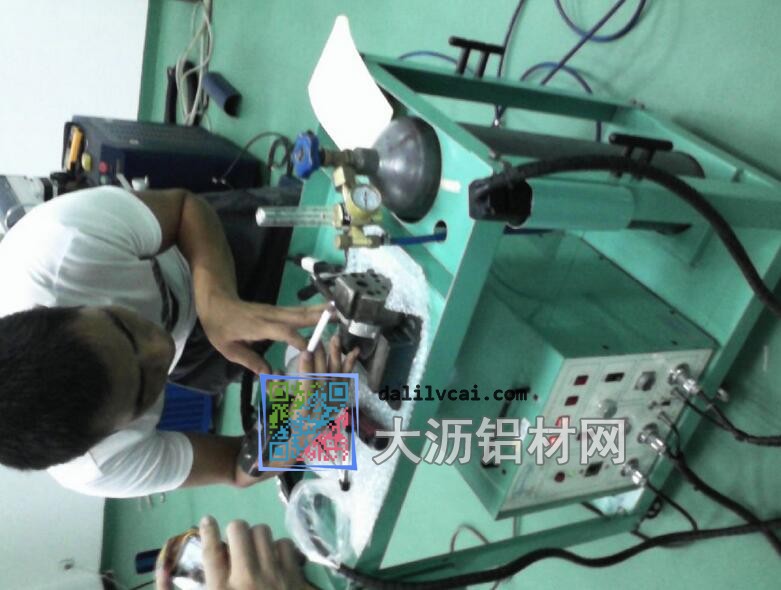
模具氮化處理現(xiàn)場
傳統(tǒng)的合金鋼料中之鋁、鉻、釩及鉬元素對滲氮甚有幫助。這些元素在滲氮溫度中,與初生態(tài)的氮原子接觸時,就生成安定的氮化物。尤其是鉬元素,不僅作為生成氮化物元素,亦作為降低在滲氮溫度時所發(fā)生的脆性。其他合金鋼中的元素,如鎳、銅、硅、錳等,對滲氮特性并無多大的幫助。一般而言,如果鋼料中含有一種或多種的氮化物生成元素,氮化后的效果比較良好。其中鋁是最強(qiáng)的氮化物元素,含有0.85~1.5%鋁的滲氮結(jié)果最佳。在含鉻的鉻鋼而言,如果有足夠的含量,亦可得到很好的效果。
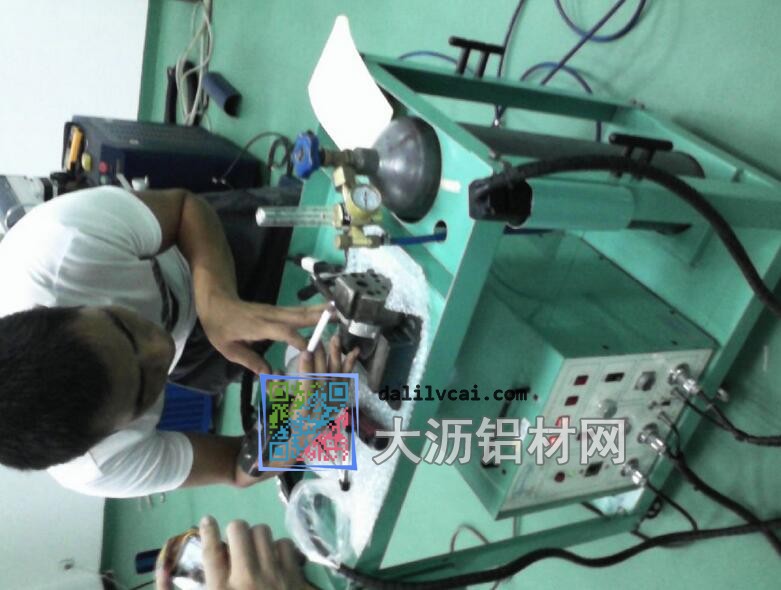
模具氮化處理現(xiàn)場
1滲氮層硬度過低
原因———氮化鋼化學(xué)成分不符或混料;鋼件未經(jīng)調(diào)質(zhì)預(yù)處理,未獲得氮化前所需細(xì)密的回火索氏體組織,或雖經(jīng)調(diào)質(zhì)預(yù)處理,但基體組織硬度低,滲氮硬化層如附在薄冰上;控溫儀表失靈,導(dǎo)致氮化溫度過高和氮化強(qiáng)滲期NH3分解率偏高,爐內(nèi)氮?dú)夥者^低或氮化箱內(nèi)氨氣含水過量,對NH3分解起“一觸媒”作用。生產(chǎn)實(shí)踐表明,當(dāng)NH3分解率≥65%~70%時,介質(zhì)中氫氣含量增加,會阻礙工件表面氮化物形核,降低工件表面吸氮能力,鋼件表層含氮量低,滲氮件表面有油污、氧化皮和脫碳層未去除,或使用新的滲氮罐及滲氮罐久用未經(jīng)退氮;滲氮爐密封不嚴(yán)、漏氣等,都會造成氮化層硬度過低。
措施———嚴(yán)格檢查滲氮鋼材,投產(chǎn)前對滲氮鋼進(jìn)行化學(xué)成分復(fù)查,合格后再投產(chǎn);氮化前必須對鋼件進(jìn)行調(diào)質(zhì)預(yù)處理,以獲得均勻細(xì)密的回火索氏體組織和所需硬度,調(diào)質(zhì)回火溫度應(yīng)略高于滲氮溫度,確保滲氮后鋼基體硬度不降低;選用WJ21型微機(jī)控溫儀,控溫精度在±1.5℃以內(nèi),確保滲氮溫度準(zhǔn)確無誤。滲氮前工件噴細(xì)砂處理,去除氧化皮、脫碳層和污物,并檢查滲氮爐密封性,發(fā)現(xiàn)漏氣及時修理或更換;選用搪瓷罐,對不銹鋼罐應(yīng)先空罐氮化后啟用,對久用氮化罐及工夾具要退氮后再用;氮化過程中要緩慢升溫加熱,適當(dāng)加大NH3流量,降低NH3分解率使之≤50%。返修時清理干凈滲氮工件表面后,修訂氮化工藝,補(bǔ)滲氮一次,以達(dá)到技術(shù)要求。
2滲氮層淺
原因———滲氮爐有效加熱區(qū)溫差大,且不均勻;鋼件表面有油污,滲氮件裝爐不當(dāng);鋼件之間過密,甚至層疊,使進(jìn)氣管道堵塞,氣流不暢;第一階段強(qiáng)滲期,NH3分解率不穩(wěn)定,有時過高,有時過低;第二階段擴(kuò)散溫度過低、保溫時間不足等因素都會造成滲氮層淺,且不均勻。
措施———疏通管道閥門,穩(wěn)定控制NH3分解率在20%~40%之間,使之產(chǎn)生的活性[N]原子基本上與鋼件表面吸[N]量及[N]的擴(kuò)散量平衡;精密控溫,有效加熱區(qū)溫差不大于±1.5℃和延長擴(kuò)散時間;滲氮件合理裝掛,保證工件間氨氣均勻暢通,滲氮爐應(yīng)嚴(yán)格密封,確保爐內(nèi)氮?dú)夥昭h(huán)正常;采用催滲氮化,滲劑中加入適量NH4Cl和RE(稀土)元素等催滲劑,選用鍍Ti氮化,鋼件表面先鍍Ti,因Ti與N親和力強(qiáng),形成Ti在Fe中固溶體,迅速形成均勻氮化層。生產(chǎn)實(shí)踐表明,新工藝與傳統(tǒng)工藝比,能迅速生成厚且均勻的氮化層,滲層深度增加25%~40%,生產(chǎn)周期縮短近一半,節(jié)電40%~50%。
返修處理,用汽油或酒精清理干凈滲氮表面,嚴(yán)格按原第二階段擴(kuò)散工藝補(bǔ)滲氮一次以達(dá)到質(zhì)量指標(biāo)。
3滲氮層硬度不均,有軟點(diǎn)
原因———原材料化學(xué)成分不均勻,偏析嚴(yán)重,晶粒粗大(≤7級),奧氏體呈長條狀;鋼中鐵素體呈大塊狀和雜質(zhì)含量超標(biāo),導(dǎo)致淬火組織粗大和塊狀鐵素體未溶解及調(diào)質(zhì)回火溫度過高;原材料脫碳層未加工和鋼件表面污物未除凈;爐內(nèi)溫度不均勻,鋼件裝掛不當(dāng),間距小,相互接觸,氣管堵塞氨氣不暢;局部滲氮鋼件鍍錫層過厚或結(jié)合不牢。風(fēng)扇轉(zhuǎn)速太快、震動大造成流錫等,上述原因會導(dǎo)致滲氮面產(chǎn)生亮塊、亮點(diǎn)、硬度等不均,由于性能不穩(wěn)定,軟點(diǎn)處硬度低,先造成磨損,形成溝槽而致使模具失效。
措施———選用爐外精煉鋼、電渣重熔鋼、真空熔煉鋼,這些材料具有純潔度高、雜質(zhì)少、晶粒細(xì)、碳化物小、化學(xué)成分和組織均勻、等向性能好等特點(diǎn);采用精密儀表控溫,分段控溫,合理布局電阻絲,確保爐膛各部位溫度均勻一致;留足冷切削加工余量去除脫碳層;合理裝掛,使鋼件之間留空隙,確保氨氣循環(huán)均勻暢通;鋼件調(diào)質(zhì)淬火加熱在真空電爐、保護(hù)氣氛爐或鹽浴爐中進(jìn)行,防止氧化脫碳;嚴(yán)格控制鍍錫層厚度,以0.010~0.015mm為宜;降低風(fēng)扇轉(zhuǎn)速,避免較大震動。返修時清理干凈滲氮層表面后,重新制訂滲氮工藝補(bǔ)滲氮一次達(dá)到質(zhì)量指標(biāo)。
4氮化鋼件畸變
原因———鋼件設(shè)計(jì)不合理,較多尖角銳邊,厚薄懸殊過大;氮化前鋼件存在較大組織應(yīng)力和機(jī)械冷加工應(yīng)力未消除;滲氮爐內(nèi)溫度不均勻,加熱升溫速度過快,鋼件出爐時冷卻速度大;鋼件裝掛不合理與滲氮面不對稱;滲氮層比容較大,產(chǎn)生組織應(yīng)力與滲氮層厚度成正比,滲氮層愈厚,產(chǎn)生組織應(yīng)力與比容愈大。
鋼件在上述多種應(yīng)力作用下易發(fā)生畸變,微量畸變可通過最后磨削加工去除,而超差畸變則影響裝配和使用壽命,甚至成為廢品,因此必須把畸變控制在公差范圍內(nèi)。
措施———改進(jìn)設(shè)計(jì),增加工藝孔和加強(qiáng)筋,用圓角代替尖角銳邊,減少應(yīng)力集中,并盡量使鋼件對稱,避免厚薄懸殊過大;氮化前在稍低于調(diào)質(zhì)回火溫度下回火1~2h,消除冷加工應(yīng)力;合理裝掛鋼件,確保氨氣循環(huán)暢通,不氮化易畸變部位留加工余量,以便氮化后去除畸變部位;鋼件低溫入爐,緩慢升溫,升溫速度以50~70℃/h為宜,冷卻時隨爐降溫至≤200℃出爐空冷,降低熱應(yīng)力與組織應(yīng)力;選擇適合滲氮方法,制訂合理滲氮工藝,對易畸變復(fù)雜鋼件選用輝光離子氮化等措施,確保氮化鋼件畸變在公差范圍內(nèi)或無畸變。返修時應(yīng)使易校正的畸變鋼件置于稍低于氮化溫度下加熱保溫,熱透后熱校正,校正后進(jìn)行400~420℃×2h去應(yīng)力退火處理。
5氮化層耐腐蝕性差
原因———當(dāng)?shù)摷砻嫘纬梢粚又旅艿?、化學(xué)穩(wěn)定性很高的ε相層(厚約0.015~0.060mm)時,鋼件有良好的抗腐蝕性能,但ε相層過薄(<0.015mm)或過厚(>0.06mm)時,均會降低抗腐蝕性能。實(shí)驗(yàn)表明,ε相層含氮量在6.1%~8.5%時均有較好抗蝕性能;但當(dāng)ε相層含氮量<6.1%或>8.5%時,均會降低抗蝕性。鋼件表面有銹蝕、污垢、刀痕、磨痕或爐內(nèi)分解率太高,產(chǎn)生活性[N]原子不足及滲氮時間短等,將會導(dǎo)致滲氮層表面氮濃度不足,無ε相層形成,或生成有孔隙ε相層,耐腐蝕性能差,降低模具使用壽命。
措施———選用DK21型氮勢控制儀,以有效控制滲氮層相組織成分,形成含氮濃度為6.1%~8.5%、厚度為0.015~0.060mm的致密ε相層;氮化模具應(yīng)預(yù)先調(diào)質(zhì)處理,細(xì)化原始組織,為形成致密ε相層創(chuàng)造組織條件;模具型面應(yīng)磨加工,降低表面粗糙度值;制訂能形成致密ε相層的氮化工藝,選定合適的NH3分解率和足夠的滲氮保溫時間;返修時拋光模具型面,清洗干凈后按修訂氮化工藝補(bǔ)滲氮一次。
6氮化鋁材模具表面氧化
原因———鋁材模具經(jīng)氮化后正常顏色是無光澤銀灰色,表面出現(xiàn)藍(lán)色、黃色或其他顏色,表明已被氧化著色,既影響外觀,又會影響表面硬度和耐磨性。造成表面氧化是因滲氮罐和爐蓋密封不嚴(yán),爐內(nèi)出現(xiàn)負(fù)壓,外部空氣倒灌爐內(nèi)和氨氣含水過多及滲氮保溫后隨爐冷卻時供NH3不足,吸入空氣或出爐溫度過高等原因。爐內(nèi)H2O、CO2、O2在加熱時便和工件中Fe發(fā)生化學(xué)反應(yīng),使其表面氧化,生成氧化鐵薄膜:
2Fe+O2→2FeO
Fe+CO2→FeO+CO↑
Fe+H2O→FeO+H2↑
同樣,若儀表失靈,爐內(nèi)溫度過高,工件在爐氣作用下,鋼中碳(C)便和爐氣發(fā)生化學(xué)反應(yīng),使鋼件脫碳:
2Fe(C)+O2→2Fe+2CO
2Fe(C)+CO2→2Fe+2CO
Fe(C)+2H2O→Fe+CH4+O2或Fe(C)+H2O→Fe+H2+CO
措施———滲氮前檢查滲氮罐及供氨系統(tǒng)密封性,發(fā)現(xiàn)漏氣應(yīng)及時修理或更換;NH3含水量應(yīng)≤0.15%為宜,干燥劑使用一次后應(yīng)更換或烘干再用,氨氣分解測定儀應(yīng)保持良好的工作狀態(tài);滲氮過程及結(jié)束冷卻時應(yīng)維持爐內(nèi)正壓,避免產(chǎn)生負(fù)壓,模具出爐溫度要≤200℃或滲氮保溫后出爐油冷。這樣既可提高抗疲勞強(qiáng)度,又可避免氧化。對已氧化著色的模具,可在拋光清除氧化色后按修訂工藝補(bǔ)滲氮一次,使其達(dá)到技術(shù)要求。
7氮化鋁材模具表面腐蝕
原因———傳統(tǒng)的氣體氮化生產(chǎn)周期長、效率低、成本高,采用NH4Cl催滲,能有效縮短生產(chǎn)周期,節(jié)電省時,增加效益。在氮化溫度下,NH4Cl分解為NH3和HCl,HCl能腐蝕掉金屬表面氧化膜,減少活性[N]原子滲入的阻力,從而加速氮化進(jìn)程。但若過量腐蝕會成為氮化缺陷,破壞表面粗糙度,形成腐蝕坑,降低抗疲勞強(qiáng)度,影響模具使用壽命。
措施———將固體NH4Cl與烘干后的石英砂按照1∶200均勻混合后,以0.6~1.0kg/m3(氮化罐容積)裝于氮化罐底部,與模具保持一定距離,避免與模具直接接觸,該措施能有效防止模具表面被腐蝕。返修時對輕微腐蝕模具經(jīng)拋光清除腐蝕表面后,用汽油或酒精清洗干凈,按正常滲氮工藝補(bǔ)滲氮2~3h,使其達(dá)到技術(shù)條件。
8滲氮層脆性大、起泡剝落有裂紋
原因———原材料有帶狀組織和非金屬夾雜物嚴(yán)重超標(biāo);設(shè)計(jì)不當(dāng),工件尖角銳邊表面積過大,活性[N]原子從多方面同時滲入,氮濃度高,形成ζ脆性相,結(jié)合不牢;滲氮介質(zhì)活性太強(qiáng),表面吸收大于擴(kuò)散,活性[N]原子堆積在金屬表面,表層含氮濃度過大(超過11.0%),形成ζ脆性相,因ζ相濃度大,滲層陡,大大削弱了滲層與基體結(jié)合力,易起泡,在外力和滲后因冷速過大產(chǎn)生較大內(nèi)應(yīng)力的共同作用下,引起氮化層剝落或產(chǎn)生裂紋;NH3含水量過大,分解率不足,強(qiáng)滲溫度過高,時間過長,或原材料組織粗大,表面脫碳等均會導(dǎo)致金屬表層濃度過大,滲氮層過陡,與基體結(jié)合不牢,使氮化層脆性大,易起泡,在外力作用下剝落和碎裂失效。
措施———選用無帶狀組織,雜質(zhì)少,晶粒細(xì),無宏觀和顯微冶金缺陷的精煉鋼;對原材料進(jìn)行鍛造,擊碎帶狀組織,細(xì)化晶粒,改變非金屬夾雜物形貌,消除偏析,使之細(xì)化與均勻分布;改進(jìn)設(shè)計(jì),將尖角銳邊改成圓角;控制供NH3量與分解率及保持爐內(nèi)正壓力,使活性[N]原子擴(kuò)散速度稍大于金屬表面吸收速度,避免出現(xiàn)高氮濃ζ脆性相;NH3流量愈大,爐內(nèi)停留時間愈長,NH3分解率愈高,氨分解率宜控在30%~50%之間;經(jīng)常更換干燥劑,使氨氣中H2O≤0.02%。采用精密多段控溫,保持爐內(nèi)溫度均勻;確保模具工作面表面粗糙度Ra為0.2μm;采用輝光離子氮化等新工藝,縮短強(qiáng)滲期,延長擴(kuò)散期,可降低滲層氮濃度,使氮化層均勻,濃度和硬度梯度由表至內(nèi)平衡降低,可消除滲氮層裂紋,增強(qiáng)滲層韌性,降低脆性和提高滲層與基體結(jié)合力,提高抗沖擊性能。返修時清理干凈滲氮表面后,置于550~560℃氮化爐中保溫10~15h,在較低NH3分解率氣氛中擴(kuò)散處理,再經(jīng)金相檢查,達(dá)到質(zhì)量標(biāo)準(zhǔn)。
9魚骨狀氮化物
原因———因氨氣含水分高,雜質(zhì)多,分解率太低,爐內(nèi)出現(xiàn)負(fù)壓,外部空氣倒灌;以及原材料原始組織中有大塊游離鐵素體未消除,都會使模具滲氮后形成魚骨狀氮化物,氮化鋼一般含碳量≤0.55%,當(dāng)鋼錠從1000~1200℃高溫奧氏體狀態(tài)經(jīng)長時間緩慢冷卻擴(kuò)散退火后,游離鐵素體沿奧氏體晶界及解理面以微細(xì)格子狀析出,晶粒粗大,調(diào)質(zhì)處理無法消除,大塊鐵素體保留在氮化過程中,因金屬表層鐵素體增大吸氮能力,使氮元素富集,導(dǎo)致氮化物沿一定晶面呈魚骨狀析出,使氮化層組織性能惡化,脆性大,無法使用。
措施———滲氮前嚴(yán)格檢查,滲氮罐及供氨系統(tǒng)應(yīng)密封無滲漏,確保滲氮過程爐內(nèi)維持正壓;氨氣含水量應(yīng)≤0.15%,并經(jīng)常更換干燥劑,徹底排除爐內(nèi)非滲氮?dú)夥?加強(qiáng)原材料原始組織檢查,不使用有大塊鐵素體組織的材料;若需利用該材料必須改鍛,擊碎粗大鐵素體組織,鍛后正火處理,進(jìn)一步細(xì)化組織,再按正常調(diào)質(zhì)預(yù)處理,以獲得氮化前所需的均勻細(xì)密回火索氏體組織。對有魚骨狀氮化物的工件,應(yīng)采取退氮處理,若有磨量,磨去魚骨狀氮化物后,按修訂工藝補(bǔ)滲氮一次,經(jīng)金相檢查組織性能合格后方可利用。
10網(wǎng)狀、波紋狀氮化物
原因———氮化時氮化物沿晶界擴(kuò)展形成網(wǎng)狀、波紋狀的氮化物工件韌性差、脆性大、耐沖擊和耐磨損性能低,服役時在外力作用下易產(chǎn)生疲勞剝落。原因是氮化前調(diào)質(zhì)預(yù)處理淬火加熱溫度太高,晶粒粗大(≤7級)和嚴(yán)重氧化脫碳;控溫儀表失靈,爐內(nèi)實(shí)際溫度大大高于儀表指示溫度,造成滲氮溫度過高,使擴(kuò)散層中氮化物聚集長大,彌散度降低;液氨含水過量,干燥劑失效和NH3分解率太低,生成過量活性[N]原子堆集于晶界。
措施———制訂合理的調(diào)質(zhì)預(yù)處理工藝,淬火加熱溫度應(yīng)確保奧氏體晶粒≥8級,在保護(hù)氣氛爐中進(jìn)行,防氧化脫碳;改進(jìn)設(shè)計(jì),以圓角代替尖角銳邊;滲氮溫度不宜超過580℃,隨爐校驗(yàn)控溫儀表,加熱和冷卻速度不宜過快;定期更換干燥劑,選用QRD2112型氨氣分解測定儀,嚴(yán)格按需控制氨分解率,避免爐氣氮勢過高等,能有效防止網(wǎng)狀、波紋狀氮化物形成。
11結(jié)束語
針對以上氮化缺陷,采取有效措施確保氮化質(zhì)量,充分發(fā)揮氮化在鋁材模具制造中強(qiáng)化效果,能有效提高鋁材模具質(zhì)量和使用壽命,給企業(yè)帶來經(jīng)濟(jì)效益。