火法——電解法是多年來處理銅陽極泥的常規(guī)方法,至今仍為國內(nèi)外所廣泛使用?,F(xiàn)行生產(chǎn)流程一般由下列工序組成:(1)除銅和硒;(2)還原熔煉產(chǎn)出貴鉛合金;(3)貴鉛氧化精煉為金銀合金,即陽極泥;(4)銀電解;(5)銀陽極泥作某些處理后,進行金電解精煉。工藝流程見圖1所示。
將銅陽極泥(含水20%~40%)送入不銹鋼混料槽,按Cu、Ag、Se、Te和硫酸進行化學(xué)反應(yīng)所需理論量的130%~140%左右,配加濃硫酸,機械攪拌成糊狀,用加料機均勻地送入回轉(zhuǎn)窯內(nèi)進行硫酸化焙燒?;剞D(zhuǎn)窯用煤氣或重油間接加熱,溫度自進料端至排料端逐漸升高。進料端溫度220~300℃,主要為爐料的干燥區(qū);中部450~550℃,主要為硫酸反應(yīng)區(qū);出料端為600~680℃,硫酸化反應(yīng)完全,SeO2揮發(fā)。窯內(nèi)保持負(fù)壓,進料端為300~500Pa,物料在窯內(nèi)(停留)3h左右,硒揮發(fā)率可達(dá)93%~97%。窯渣(脫硒渣)流入貯料斗,定時放出,渣含硒0.1%~0.3%左右。含SeO2和SO2的氣體經(jīng)進料端的氣管進入吸收塔。吸收塔分兩組,每組3個串聯(lián),兩組交換使用。塔內(nèi)裝水,爐氣中的SeO2溶于水形成H2SeO3,并被SO2還原成粉狀元素硒,經(jīng)水洗干燥得95%左右的粗硒。第一塔吸收還原率約85%,第二塔約7%~10%,第三塔約2%~6%。塔液和洗液用鐵置換后含硒低于0.05g/L棄之。含硒置換渣返回窯內(nèi)處理?;剞D(zhuǎn)窯焙燒后的窯渣用水浸出或稀硫酸浸出脫銅。浸出時固液比為1:2~3,溫度90℃以上,機械攪拌2~3h,CuSO4和AgSO4和部分硫酸碲溶于水中,脫銅渣經(jīng)水洗過濾,送金應(yīng)冶煉系統(tǒng)。溶液輸送到置換罐,加溫至90℃,用銅片將Ag、Te(硫酸根、硫酸碲)置換,直至溶液加入鹽酸不顯白色沉淀為止。沉淀經(jīng)洗滌過濾,粗銀粉送金銀冶煉系統(tǒng),硫酸銅溶液用泵輸送至銅電解車間回收銅。溶液含銅30~60g/L,浸出渣含銅1%~3%。經(jīng)硫酸化焙燒揮發(fā)硒,浸出脫銅后的浸渣成分列于表1。
浸出與置換在不銹鋼罐中進行。浸出罐Φ1200mm×600mm,機械攪拌。置換罐Φ1500mm×1600mm。
同時,也發(fā)生還原反應(yīng):
三、貴鉛的氧化精煉
最后當(dāng)Au+Ag達(dá)到95%以上即澆鑄成陽極板進行銀電解精煉,得產(chǎn)品銀和進一步提取金和鉑鈀。
氧化鉍渣在轉(zhuǎn)爐內(nèi)還原熔煉20~24h,配料一般為:蘇打3%~4%,硫化鐵20%~30%,螢石3%~4%,粉煤<3%,每爐處理量為5~6t。所得鉍合金組成為:Bi50%~65%,Pb9%~10%,Cu9%~25%,Sb2%~4%,Au+Ag3%~4%,F(xiàn)e微量。鉍直收率80%~90%。在鑄鍋中(Φ1000mm×900mm)處理,依次除去各種雜質(zhì),可得1、2號鉍。
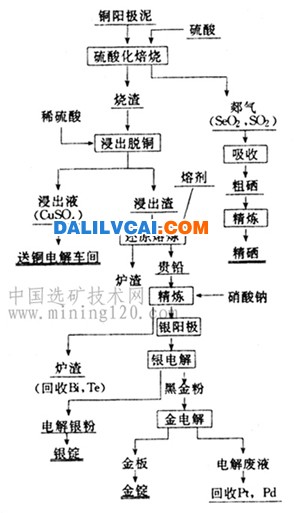
圖1 銅陽極泥火法-電解常規(guī)工藝流程
一、硫酸化焙燒
銅陽極泥之所以要首先焙燒除硒,是因為火法熔煉陽極泥時,由于硒的存在一方面會導(dǎo)致于金屬與爐渣兩相間形成一層含銀很高的硒冰洞,而回收硒冰洞中的銀需要延長吹風(fēng)氧化時間,從而延長生產(chǎn)周期。另一方面,硒會分散于爐渣、冰洞和貴鉛中,給硒的回收帶來困難。
銅陽極泥硫酸化焙燒的主要目的是把硒氧化成SeO2使之揮發(fā),進入吸收塔的水溶液中變?yōu)镠2SeO3,然后被爐氣中的SO2還原而生成元素硒粉;銅轉(zhuǎn)化為可溶性的CuSO4,硫酸化焙燒渣進行水浸出(或稀硫酸)脫銅。脫銅渣進入金銀冶煉系統(tǒng),浸銅液用銅板置換銀,將粗銀粉送金銀系統(tǒng),硫酸銅送至銅電解車間回收銅。
(一)焙燒設(shè)備——回轉(zhuǎn)窯及吸收塔
回轉(zhuǎn)窯日處理陽極泥(濕泥)1.5t?;剞D(zhuǎn)窯由16mm鍋爐鋼板焊接制成,其尺寸為Φ750mm×10800mm,轉(zhuǎn)速65r/s,傾斜度不超過2%,內(nèi)壁無爐襯,為防止?fàn)t料粘壁,窯內(nèi)裝-Φ75mm帶耙齒的圓鋼攪籠,翻動陽極泥。窯外用耐火磚砌一火室,采用外加熱法,即整個窯身置于燃燒室內(nèi),用煤氣(或重油)加熱。窯和吸收塔用水環(huán)真空泵保持負(fù)壓。吸收塔為鐵塔內(nèi)襯鉛,吸收塔尺寸為Φ(1000~1200)mm×(600~800)mm。一般一塔為Φ1200mm×800mm,二、三塔為Φ1000mm×600mm。
(二)處理過程
將銅陽極泥(含水20%~40%)送入不銹鋼混料槽,按Cu、Ag、Se、Te和硫酸進行化學(xué)反應(yīng)所需理論量的130%~140%左右,配加濃硫酸,機械攪拌成糊狀,用加料機均勻地送入回轉(zhuǎn)窯內(nèi)進行硫酸化焙燒?;剞D(zhuǎn)窯用煤氣或重油間接加熱,溫度自進料端至排料端逐漸升高。進料端溫度220~300℃,主要為爐料的干燥區(qū);中部450~550℃,主要為硫酸反應(yīng)區(qū);出料端為600~680℃,硫酸化反應(yīng)完全,SeO2揮發(fā)。窯內(nèi)保持負(fù)壓,進料端為300~500Pa,物料在窯內(nèi)(停留)3h左右,硒揮發(fā)率可達(dá)93%~97%。窯渣(脫硒渣)流入貯料斗,定時放出,渣含硒0.1%~0.3%左右。含SeO2和SO2的氣體經(jīng)進料端的氣管進入吸收塔。吸收塔分兩組,每組3個串聯(lián),兩組交換使用。塔內(nèi)裝水,爐氣中的SeO2溶于水形成H2SeO3,并被SO2還原成粉狀元素硒,經(jīng)水洗干燥得95%左右的粗硒。第一塔吸收還原率約85%,第二塔約7%~10%,第三塔約2%~6%。塔液和洗液用鐵置換后含硒低于0.05g/L棄之。含硒置換渣返回窯內(nèi)處理?;剞D(zhuǎn)窯焙燒后的窯渣用水浸出或稀硫酸浸出脫銅。浸出時固液比為1:2~3,溫度90℃以上,機械攪拌2~3h,CuSO4和AgSO4和部分硫酸碲溶于水中,脫銅渣經(jīng)水洗過濾,送金應(yīng)冶煉系統(tǒng)。溶液輸送到置換罐,加溫至90℃,用銅片將Ag、Te(硫酸根、硫酸碲)置換,直至溶液加入鹽酸不顯白色沉淀為止。沉淀經(jīng)洗滌過濾,粗銀粉送金銀冶煉系統(tǒng),硫酸銅溶液用泵輸送至銅電解車間回收銅。溶液含銅30~60g/L,浸出渣含銅1%~3%。經(jīng)硫酸化焙燒揮發(fā)硒,浸出脫銅后的浸渣成分列于表1。
表1 焙燒浸出脫銅后浸渣成分(%)
廠別
|
Cu
|
Pb
|
As
|
Sb
|
Bi
|
Se
|
Te
|
Au
|
Ag
|
SiO2
|
其它
|
一廠
二廠
|
<3
1.48
|
15~20
9.63
|
2.0~3.7
0.86
|
3~14
0.41
|
0.59
2.03
|
0.03~0.04
1.62
|
0.4
0.13
|
1~1.5
0.14
|
12~15
21.86
|
14.7
9
|
余額
余額
|
浸出與置換在不銹鋼罐中進行。浸出罐Φ1200mm×600mm,機械攪拌。置換罐Φ1500mm×1600mm。
焙燒除硒通常還有用氧化焙燒和蘇打燒結(jié)焙燒方法。氧化焙燒根據(jù)實踐證明與收塵設(shè)備有關(guān),而且爐氣中(從陽極泥中來的)所含的金屬銅粉、沒燃燒完的煤煙和SO2等與亞硒酸作用,發(fā)生一系列副反應(yīng),把亞硒酸還原成金屬硒,或生成不溶性的硒化物沉淀,而降低硒的回收率,且焙燒煙塵中往往導(dǎo)致貴金屬的損失。因此氧化焙燒已多時不用。蘇打燒結(jié)焙燒法硒的回收率在90%以上。但由于碲也大部分生成亞碲酸鈉,當(dāng)用熱水浸出時,碲會和硒一道進入溶液,進而難以分離碲硒,不易獲得高純硒,因此蘇打燒結(jié)焙燒法不適于處理含碲高的陽極泥。
二、還原熔煉產(chǎn)出貴鉛合金
銅陽極泥脫銅浸出渣的熔煉,過去曾用反射爐或平爐。目前,國內(nèi)外廣泛使用轉(zhuǎn)爐或電爐。浸出渣加入還原劑和熔劑,經(jīng)還原熔煉,產(chǎn)出含金、銀總量30%~40%的貴金屬與鉛的合金(俗稱貴鉛)。故熔煉作業(yè)的冶金爐俗稱為貴鉛爐。
(一)設(shè)備——圓筒形臥式轉(zhuǎn)爐
還原熔煉在轉(zhuǎn)爐中進行,爐子的尺寸見表2,例如二廠轉(zhuǎn)爐,外殼用16mm厚鍋爐鋼板卷焊而成,尺寸為562400mm×4200mm,爐床面積5.5m2,出煙口620mm×520mm,床能力(處理陽極泥)1~1.2t/(m2·d),機械傳動,轉(zhuǎn)數(shù)12r/min。自爐殼向爐心襯以10mm石棉板兩層,全爐徑向立砌一層鋁鎂磚,爐底用鎂砂粉、耐火泥焦粉混合物墊高400mm,爐壽命200爐次以上,爐子使用前應(yīng)經(jīng)烤爐和洗爐。新砌的轉(zhuǎn)爐或修理或停產(chǎn)再生產(chǎn),均應(yīng)進行烤爐,使?fàn)t溫逐漸升高,以保護爐內(nèi)砌體,延長爐齡。洗爐,是向爐內(nèi)加入廢鉛或氧化鉛煙塵(加煙塵洗爐應(yīng)配入焦屑,碳酸鈉和螢石等還原劑和熔劑),使?fàn)t內(nèi)磚縫充滿鉛,以提高金、銀的直收率。洗爐完畢,將鉛放出鑄錠供下次再用。
表2 轉(zhuǎn)爐主要尺寸實例
名稱
|
一廠
|
二廠
|
三廠
|
四廠
|
爐子直徑/mm
爐子長度/mm
加料量/t·爐-1
操作周期/h·爐-1
轉(zhuǎn)動方式
|
2500
2770
2
17
機械傳動
|
2400
4200
5
27
機械傳動
|
1200
1830
0.4
10
手動
|
1300
1800
0.25
8~10
手動
|
(二)脫硒脫銅后浸出渣的熔煉
熔煉脫硒、銅浸出渣,是向洗爐后的爐中加入浸出渣,經(jīng)還原熔煉產(chǎn)出貴鉛錠。如某廠脫銅、硒浸出渣的組分為:H2O30%、Au1%~1.5%、Ag10%~15%、Pb15%~20%、Cu<5%、Se<0.3%、Te0.4%、SiO2<5%。熔煉時配入8%~15%碳酸鈉、3%~5%螢石粉、6%~10%碎焦屑(或粉煤)、2%~4%鐵屑。蘇打的加入量也可以按SiO2含量的1.8倍或稍過量配入。在熔煉過程中,如爐結(jié)太厚或粘渣過多,則適當(dāng)增加蘇打量(若稀渣過多則減少)。由于貴鉛熔煉是在微還原氣氛中進行的,故還原劑(碎焦或煤粉)的加入量應(yīng)按還原浸出渣中所含的銅、鎳及部分鉛的需要計算加入(實際生產(chǎn)中根據(jù)生產(chǎn)實際經(jīng)驗配料),不使其過量。如過量過大,則會使大量雜質(zhì)一起還原進入貴鉛中,而降低貴鉛中金、銀的含量。
銅陽極泥經(jīng)提硒脫銅后的浸出渣,配以石灰、蘇打、螢石、鐵屑作熔劑,煤粉或焦粉作還原劑,均勻混合后,經(jīng)皮帶運輸機送入轉(zhuǎn)爐內(nèi)。爐內(nèi)保持負(fù)壓(30~100Pa)。以重油為燃料,重油預(yù)熱至60℃以上,用壓力為16kPa以上的空氣送入爐內(nèi)霧化燃燒。熔化期溫度保持在1200~1300℃,氧化期溫度保持在700~900℃。
爐料入爐后,逐漸升溫,除去水分,氧化物(As、Sb、Pb等)相繼揮發(fā)而進入爐氣。爐料開始熔化。并發(fā)生造渣反應(yīng):
Na2COa﹦Na2O+CO2
Na2O+As2O5﹦Na2O·As2O5
Na2O+Sb2O5﹦Na2O·Sb2O5
Na2O+SiO2﹦Na2O·SiO2
PbO+SiO2﹦PbO·SiO2
CaO+SiO2﹦CaO·SiO2
同時,也發(fā)生還原反應(yīng):
2PbO+C﹦2Pb+CO2
PbO+Fe﹦Pb+FeO
PbSO4+4Fe﹦Fe3O4+FeS+Pb
PbS+Fe﹦Pb+FeS
Ag2S+Fe﹦2Ag+FeS
陽極泥中的金、銀被還原出來的金屬鉛熔體所捕集,形成貴鉛,其反應(yīng)可用下式表示:
Pb+Ag+Au﹦Pb(Ag+Au)
貴鉛熔體與爐渣互不溶解,密度差又大,故爐渣浮在熔池表面,貴鉛沉于熔池下層。為了提高貴鉛中金、銀的品位,把爐渣放出,繼續(xù)往貴鉛熔體中鼓入空氣,使其中的As、Sb、Cu、Bi等雜質(zhì)氧化,As、Sb形成低價氧化物時,揮發(fā)進入爐氣(4As+3O2﹦2As2O3↑),(4Sb+3O2﹦2Sb2O3↑)。若進一步氧化形成高價氧化物(2Sb2O3+2O2→2Sb2O5),可與堿性氧化物造渣(Na2O+2Sb2O5﹦Na2O·Sb2O5)。
全爐作業(yè)時間為18~24h。貴鉛產(chǎn)出率為30%~40%,成分為:Au0.2%~4.0%,Ag25%~60%,Bi10%~25%,Te0.2%~2.0%,Pb15%~30%,As3%~10%,Sb5%~15%,Cu1%~3%。稀渣產(chǎn)出率25%~35%,含Au<0.01%、Ag<0.2%、Pb15%~45%,送往鉛冶煉系統(tǒng)回收Pb,或者送鼓風(fēng)爐富集后再入貴鉛爐熔煉銅銀合金。粘渣和氧化渣(后期渣)含Au、Ag較高,返回還原熔煉。煙氣經(jīng)濕法收塵后放空,所得的煙塵作提取As、Sb的原料。
(三)日立冶煉廠陽極泥浸出渣的電爐熔煉
日本礦業(yè)公司日立冶煉廠為了提高金、銀的直收率,減少中間產(chǎn)品、縮短熔煉工時及流動資金的積壓,改用電爐熔煉陽極泥脫銅浸出渣并用新的電爐配料,使電爐至分銀爐熔煉過程中需返回處理的中間產(chǎn)品由6種(電爐冰銅、氧化鉛貴鉛、氧化鉛冰銅、氧化鉛、分銀爐渣、硝石碳酸鈉渣)減少至3種(氧化鉛分銀爐渣等),且大大降低了各中間產(chǎn)品的金、銀含量。據(jù)改進配料后統(tǒng)計,爐料的金、銀品位及產(chǎn)品的數(shù)量、品位和回收率都大大提高,金銀回收率達(dá)99.3%以上。
三、貴鉛的氧化精煉
還原熔煉所得貴鉛含金銀一般在35%~60%范圍內(nèi),余為Pb、Cu、As、Sb等雜質(zhì),氧化精煉在轉(zhuǎn)爐溫度為900~1200℃的條件下,鼓入空氣和加入熔劑、氧化劑等,使絕大部分雜質(zhì)氧化成不溶于金銀的氧化物,進入煙塵和形成爐渣除去,得到含金銀90%以上,適合于銀電解的陽極板。
在貴鉛氧化精煉過程中,貴鉛中各種金屬的氧化順序為:Sb、As、Pb、Bi、Cu、Te、Se、Ag。貴鉛中一般含鉛較多,也易氧化,所以氧化精煉時,實際上主要以PbO充當(dāng)氧的傳遞劑,把砷、銻氧化(2Pb+O2﹦2PbO,2Sb+3PbO﹦Sb2O3+3Pb,2As+3PbO﹦As2O3+3Pb),這些砷、銻的低價氧化物和部分PbO易于揮發(fā)而進入煙氣,經(jīng)布袋收塵后所得煙塵返回熔煉處理。As2O3、Sb2O3亦可進一步氧化成高價氧化物(Sb2O5、As2O5),并與堿性氧化物(PbO、Na2O等)造渣,或直接形成亞砷(或銻)酸鉛(3PbO+Sb2O5﹦3PbO·Sb2O5,2As+ 6PbO﹦3PbO·As2O3+3Pb,2Sb+6PbO﹦3PbO·Sb2O3+3Pb),亞砷(銻)酸鉛與過量空氣接觸時,也可形成砷(銻)酸鉛(3PbO·As2O3+O2﹦3PbO·As2O5)。
由于As2O5的離解壓比Sb2O5低,所以多數(shù)以砷酸鹽形態(tài)進入爐渣,而銻則多數(shù)揮發(fā)進入爐氣。當(dāng)砷銻氧化基本完成后(即不冒白煙),改為表面吹風(fēng)繼續(xù)進行氧化精煉,可以把鉛全部氧化除去。
Cu、Bi、Te、Se等的較難氧化的金屬,即難以用PbO氧化。但當(dāng)As、Sb、Pb都氧化除去后,再繼續(xù)氧化精煉,鉍就發(fā)生氧化(4Bi+3O2﹦2Bi2O3),生成含部分銅、銀、砷、銻等雜質(zhì)的鉍渣,經(jīng)沉淀熔煉以降低含銀量后,即作為回收鉍的原料。
當(dāng)爐內(nèi)合金達(dá)到Au+Ag﹦80%以上時,即加入貴鉛量5%的Na2CO3和1%~3%的NaNO3,用人工強烈攪拌,使銅、碲、硒徹底氧化(2NaNO3﹦Na2O+2NO2+[O],2Cu+[O]﹦Cu2O,Me2Te+8NaNO3﹦2MeO+8NO2+TeO2+4Na2O,MeSe2+8NaNO3﹦2MeO+8NO2+SeO2)。TeO2與加入的Na2CO3形成亞碲酸鈉,即形成所謂蘇打渣(碲渣)(TeO2+Na2CO3﹦Na2TeO3+CO2↑),用作回收碲的原料。
最后當(dāng)Au+Ag達(dá)到95%以上即澆鑄成陽極板進行銀電解精煉,得產(chǎn)品銀和進一步提取金和鉑鈀。
氧化精煉用重油加熱,每爐作業(yè)為45~72h。轉(zhuǎn)爐用12mm鍋爐鋼板制成,外殼尺寸為Φ600mm×2240mm,爐床面積1.5m2,床能力(貴鉛)1.6t/(m2·d),爐底墊高100mm,徑向立砌一層鎂磚。
四、鉑、鈀的回收
金電解液使用一段時間(約2~3個月)后,雜質(zhì)積累,不能再繼續(xù)使用,其中的金用硫酸亞鐵、草酸或二氧化硫還原沉出,鑄成陽極板返回金電解。溶液含Pt5~15g/L,Pd15~30g/L,送去回收鉑、鈀。首先用NH4CL沉鉑得氯鉑酸銨,經(jīng)煅燒得鉑精礦。溶液用鋅片置換得鈀精礦。鉑、鈀精礦經(jīng)精煉提純后即得純海綿鉑、鈀。
五、其他有價成分的綜合回收
銅陽極泥中除了貴金屬外,還有一些有價成分,必需予以綜合回收。一般,著重回收的有碲、鉍、硒;對于砷、銻除本身價值外,更重要的是為了消除它們對環(huán)境的污染,故也必須予以回收。
(一)碲的回收:貴鉛火法氧化精煉后期產(chǎn)出的蘇打渣,含碲5%~15%,其余成分為:Se0.2%~1.0%,Cu3%~10%,Pb3%~8%,Bi10%~20%,SiO25%~15%。
蘇打渣濕磨液固比為2~3,室溫磨6h,至-80目;水稀釋4~5倍浸出,加熱至80℃以上澄清過濾;溶液用Na2S,CaCl2凈化后渣返球磨,溶液以稀H2SO4中和至pH=5(>80℃),澄清過濾得含65%以上的TeO2;TeO2用水洗凈后,用NaOH溶解制備成電解液(NaOH90~100g/L,Te150~300g/L,Pb<0.1g/L,Se<1.5g/L)電解,得陰極碲(含量>98%),然后鑄錠,產(chǎn)出99%~99.9%的碲。
(二)鉍的回收:金銀氧化精煉產(chǎn)出的氧化鉍渣,組成為:Bi14%~35%,Pb15%~25%,Cu10%~20%,Sb10%~14%,As<0.005%,Ag1%~3%,SiO215%~25%。
氧化鉍渣在轉(zhuǎn)爐內(nèi)還原熔煉20~24h,配料一般為:蘇打3%~4%,硫化鐵20%~30%,螢石3%~4%,粉煤<3%,每爐處理量為5~6t。所得鉍合金組成為:Bi50%~65%,Pb9%~10%,Cu9%~25%,Sb2%~4%,Au+Ag3%~4%,F(xiàn)e微量。鉍直收率80%~90%。在鑄鍋中(Φ1000mm×900mm)處理,依次除去各種雜質(zhì),可得1、2號鉍。
(三)砷的回收:濕法收塵收集的熔煉煙塵,一般成分為:As10%~25%,Sb20%~35%,Pb8%~12%,F(xiàn)e1%,Bi2%~4%,Te0.2%~0.4%,Au<0.001%,Ag0.2%~0.4%,H2O25%~35%。
熔煉煙塵拌蘇打焙燒—浸出—過濾—濾液濃縮結(jié)晶得到砷酸鈉產(chǎn)品。砷酸鈉成分為:As12%~17.6%,Sb<0.1%,F(xiàn)e<0.01%,Na2CO325%~30%,Pb微量,Bi微量。結(jié)晶效率為88%~90%。
(四)銻的回收:熔煉煙塵浸出砷后,其成分為:As1.7%~3.0%,Sb40%~60%,Pb13%~20%,H2O30%~40%,Na2CO35%~7%。
浸砷后渣拌粉煤、蘇打,經(jīng)還原熔煉,氧化揮發(fā),再還原、精煉得精銻。