強化溶出新技術有:(1)管道化溶出;(2)單管預熱-高壓釜溶出;(3)管道化加熱-停留罐溶出。
一、管道化溶出
管道化溶出就是“溶出過程在管道中進行,且熱量通過管壁傳給礦漿”的溶出。有單流法和多流法兩種。德國采用單流法,匈牙利采用多流法。
1980年RA-6管道化溶出裝置在Nab廠投產,采用圖1所示的工藝流程。LWT表示原礦漿-溶出礦漿熱交換管,外管Φ368mm,內裝4根Φ100mm管,共長160mm。BWT(1~8)是溶出礦漿經八級自蒸發(fā)產生的二次蒸汽與原礦漿進行交換的管,有200×10=2000m。BWT(1~6)的外管直徑為400mm,BWT(7~8)的則為508mm,內裝4根Φ100mm管。E(1~8)為八級溶出礦漿自蒸發(fā)器,E(1~6)的規(guī)格為Φ2200mm×Φ4500mm,E(7)Φ2600mm×Φ4500mm,E(8)Φ2200mm×Φ4500mm。K(0~7)為八級冷凝水自蒸發(fā)器,K(0~3)的規(guī)格為Φ1000mm×Φ1400mm,K(4~6)Φ1400mm×Φ1800mm,K(7)Φ3300mm×5000mm。
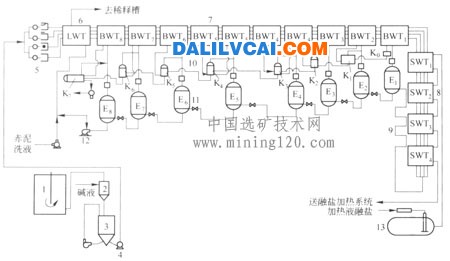
圖1 RA-6管道化溶出流程
1-礦水槽;2、3-混合槽;4-泵;5-高壓泵;6、8-管式加熱器;
9-保溫反應器;10-冷凝水自蒸發(fā)器;11-礦漿自蒸發(fā)器;12-泵;13-融鹽槽
原礦漿經LWT管加熱到90℃,在BWT管中加熱到220℃,再往SWT管中加熱到280℃,經反應器充分溶出后,到八級自蒸發(fā)和LWT換熱系統(tǒng)降溫后排出。RA-6管道化溶出裝置還配有檢測、控制和數據處理系統(tǒng)。管道化溶出技術在德國用于處理三水鋁石型和一水軟鋁石型鋁土礦。獲得較好的經濟指標。
1984年11~12月在Nab用RA-6裝置對我國山西孝義一水硬鋁石型鋁土礦進行了工業(yè)試驗。礦石成分(%):Al2O366.7,SiO212.27,F(xiàn)e2O32.08,TiO22.74,CaO0.68,灼堿14.4。礦物組成(%):一水硬鋁石68.2,高嶺石24.9,針鐵礦2.3銳鈦礦2.6,金紅石0.4,方解石0.7。工業(yè)生產用堿液為種分母液Na2Ok。濃度152.3g/L,苛性比2.76。要得到90%以上的氧化鋁溶出率及1.50以下的溶出苛性比,就必須按以下要求操作:溫度為280℃,時間為10min,添加CaO6%。原鄭州鋁廠于1990年購入Nab的RA-6型管道化溶出裝置,用于處理鋁硅比7.58的鋁土礦。在原有保溫反應管后串聯(lián)Φ1200mm×Φ1200mm的6個停留罐,礦漿流量300m3/h,使氧化鋁溶出率從69%提高到80%,每生產1t氧化鋁的脫硅、溶出、蒸發(fā)的熱耗由19GJ降至10.3GJ。
與RA-6管道化溶出過程不同,匈牙利采用多流管道化溶出裝置,即堿液和預脫硅的礦漿分別用高壓泵送入管式反應器中,先用高溫礦漿產生的二次蒸汽加熱至215℃,再用新蒸汽加熱至溶出溫度(240~260℃)。已加熱的礦漿和堿液在混合管中合流充分溶出,之后進入多級自蒸發(fā)系統(tǒng)降溫,排出反應器后進入稀釋槽。匈牙利用這套裝置處理一水軟鋁石型鋁土礦(成分(%):Al2O350、SiO26.67、Fe2O322.8),氧化鋁的溶出率為85%。所用的技術條件為:溶出溫度248℃,礦漿流量120m3/h,Na2Ok濃度為200g/L,溶出液苛性比為1.44。匈牙利的多流管道化液出裝置的主要問題是堿液結疤,后來也改為單流法。
二、單管預熱-高壓釜溶出
廣西平果鋁業(yè)公司從法國引起了單管預熱-高壓釜溶出技術,溶出系統(tǒng)流程如圖2所示。固體含量300g/L的礦漿在Φ8000mm×Φ8000mm的礦漿槽加熱至100℃,用高壓橡膠隔膜泵送入五級長2400m的單管預熱器(外管Φ336mm,內管Φ253mm),用后五級自蒸發(fā)器產生的蒸汽加熱礦漿至155℃。隨后進入中溫脫硅器分段保溫(同時也加熱)停留20min脫硅,即到5臺Φ2.8m×16m的加熱高壓釜,用前五級自蒸發(fā)器產生的蒸汽加熱礦漿至200℃。再進入6臺Φ2.8m×Φ16m的反應高壓釜,用6MPa的新蒸汽加熱礦漿至260℃。然后在3臺Φ2.8m×Φ16m的終端高壓釜中,保溫反應45~60min。溶出礦漿經十級自蒸發(fā)降溫到130℃以下,經緩沖現(xiàn)槽進入稀釋槽稀釋。加熱高壓釜和反應高壓釜都配有機械攪拌及加熱管束,終端高壓釜只有機械攪拌裝置。
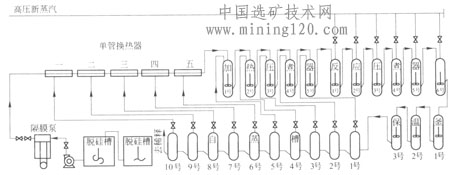
圖2 廣西平果鋁業(yè)公司從法國引進的單管預熱-高壓釜溶出流程圖
單管預熱-高壓釜溶出裝置用于處理一水硬鋁石型鋁土礦,礦漿流量為450m3/h,設計年產氧化鋁33萬t。廣西平果鋁業(yè)公司用該設備于1998年生產38萬t氧化鋁。溶出液的αk為1.50,蒸發(fā)母液的Na2Ok濃度為230g/L,氧化鋁的相對溶出率達91%。工業(yè)生產表明溶出效果好,存在的問題是磨損嚴重,需要定期頻繁停產檢修。
三、管道化加熱-停留罐溶出
管道化加熱時礦漿在管道內高速流動,雷諾系數Re達到105,處于高度湍流狀態(tài),傳熱系數達8000kJ/(m2·h·℃),比列管式熱交換器高5倍,所需熱交換面積減少。然而,對于一水硬鋁石型鋁土礦,即便溶出溫度達310℃,若沒有充足的停留時間,氧化鋁的溶出率是很低的,管道化溶出的停出時間要延長,管道就會長得難以經濟擺布。為此提出了管道化加熱-停留罐溶出強化技術。
1988年廣西平果鋁業(yè)公司的鋁土礦進行管道化加熱-停留罐溶出的結果為:堿液濃度為Na2Ok230g/L,石灰添加量為7%~10%,管式反應器預熱時間為10~12min,停留罐溶出時間為40min,氧化鋁的相對溶出率達92%,溶出液的αk為1.50。管道化加熱-停留罐溶出技術對我國其他礦的試驗也收到良好效果。