前言:
為了響應(yīng)國家節(jié)能減排號(hào)召,進(jìn)一步降低公司生產(chǎn)成本,保持設(shè)備安全、優(yōu)質(zhì)、經(jīng) 濟(jì)運(yùn)行。針對(duì)我公司A5、A6兩臺(tái)時(shí)效爐在運(yùn)行中存在溫升曲線差、電耗和天然氣消耗過大等問題,對(duì)時(shí)效爐能耗高的具體原因進(jìn)行分析并進(jìn)行節(jié)能降耗改造意義重大。時(shí)效爐能耗高的原因有很多,本文通過對(duì)我公司時(shí)效爐能耗高的主要原因進(jìn)行分析,對(duì)時(shí)效爐在升溫和保溫階段,循環(huán)風(fēng)機(jī)的最佳轉(zhuǎn)速控制進(jìn)行深入研究,通過修改PLC程序和變頻器參數(shù),合理控制風(fēng)機(jī)轉(zhuǎn)速,達(dá)到節(jié)約能耗目的。
1、鋁型材時(shí)效爐用途及結(jié)構(gòu)簡(jiǎn)介。
1.1、設(shè)備用途。
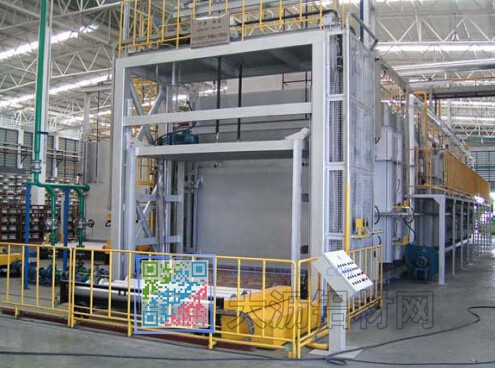
鋁合金時(shí)效爐主要用于鋁合金型材的時(shí)效處理。通過時(shí)效處理,可以使鋁合金強(qiáng)度和硬度大幅度提高,同時(shí)可以減少鋁合金材料的應(yīng)力集中、變形等問題。
1.2、時(shí)效爐結(jié)構(gòu)簡(jiǎn)介。 我公司時(shí)效爐主要由保溫爐體、爐門裝置、加熱系統(tǒng)、熱風(fēng)循環(huán)系統(tǒng)、臺(tái)車裝置及電氣控制系統(tǒng)等部分組成。 加熱系統(tǒng)采用1臺(tái)瑞典百通BG600燃?xì)馊紵龣C(jī),燃料為壓縮天然氣。為確保爐溫均勻性,爐體頂部設(shè)75KW離心式循環(huán)風(fēng)機(jī)1臺(tái),并合理配置爐內(nèi)熱風(fēng)循環(huán)導(dǎo)流系統(tǒng),使?fàn)t內(nèi)氣流分配均勻,爐內(nèi)溫差小,又保證了加熱速度與加熱質(zhì)量。爐體采用內(nèi)外兩層鋼板焊接而成的全金屬形結(jié)構(gòu),中間均勻填充硅酸鋁耐火纖維保溫,降低爐壁溫升。爐門采用電動(dòng)式升降爐門,爐門壓緊采用氣動(dòng)聯(lián)桿式四點(diǎn)平衡壓緊機(jī)構(gòu)。臺(tái)車牽引機(jī)構(gòu)采用鏈條式。
1.3、溫控系統(tǒng) 由觸摸屏、S7-200PLC、四支熱電偶、8通道無紙溫度記錄儀組成。升溫溫度、保溫溫度、升溫時(shí)間、保溫時(shí)間可分別在觸摸屏上進(jìn)行設(shè)置。 溫度控制采用級(jí)聯(lián)控制方式,即由4支溫度熱電偶采集的時(shí)效爐內(nèi)溫度信號(hào)送入PLC的閉環(huán)控制模塊經(jīng)冷端補(bǔ)償,線性化處理,與觸摸屏給定值一起經(jīng)運(yùn)算,其結(jié)果與爐溫度熱電偶采集的溫度信號(hào),再經(jīng)PLC運(yùn)算處理后,輸出給燃?xì)馊紵龣C(jī),從而控制火焰大小,達(dá)到溫度自動(dòng)調(diào)節(jié)的目的。同時(shí)通過PLC程序控制模擬量輸出模塊,輸出DC0-10V模擬量至變頻器,變頻器輸出相應(yīng)的頻率來控制循環(huán)風(fēng)機(jī)的轉(zhuǎn)速,以改變爐內(nèi)空氣的對(duì)流速度,使?fàn)t內(nèi)空氣溫度達(dá)到均勻化,完成鋁型材時(shí)效的目的。
2、興發(fā)鋁業(yè)技改前時(shí)效爐設(shè)備的現(xiàn)狀:
興發(fā)鋁業(yè)擠壓車間A5、A6時(shí)效爐均由某公司制造,加熱系統(tǒng)均采用1臺(tái)BG600天然氣燃燒機(jī),目前我公司主要時(shí)效的型材為6061和6082,升溫時(shí)間一般設(shè)定為1小時(shí)左右,保溫時(shí)間一般設(shè)定為6.5-7.5小時(shí)。每臺(tái)時(shí)效爐主要用電設(shè)備為75KW三相異步通風(fēng)機(jī)1臺(tái),采用PLC+變頻器自動(dòng)控制風(fēng)機(jī)的轉(zhuǎn)速,廠家設(shè)計(jì)的風(fēng)機(jī)轉(zhuǎn)速控制程序?yàn)樵陲L(fēng)機(jī)換向時(shí)程序輸出的頻率為52.9HZ,不換向時(shí)輸出頻率為57.02HZ。平均每噸鋁材時(shí)效耗電量為36KWh/噸。 天然氣平均耗氣量為10.3 m3 /噸。 我們通過多次溫度在線測(cè)量(參考7.4項(xiàng)升溫曲線圖),發(fā)現(xiàn)在升溫階段各部位溫差較大,在保溫階段曲線不夠平直,證明該時(shí)效爐溫度控制效果不理想。
3、時(shí)效爐能耗高的一般原因分析
由時(shí)效爐的結(jié)構(gòu)可以看出,時(shí)效爐的能源消耗主要包括由于加熱所產(chǎn)生的天然氣消耗和75KW循環(huán)風(fēng)機(jī)產(chǎn)生的電能消耗。
導(dǎo)致能耗高的可能原因分析如下:
3.1、時(shí)效爐爐體保溫效果差。 當(dāng)爐體保溫效果差時(shí),會(huì)使?fàn)t內(nèi)熱空氣通過熱傳導(dǎo)輻射到爐周圍空氣中,這勢(shì)必會(huì)造成升溫速度慢,不能滿足時(shí)效爐時(shí)效前期快速升溫的要求,同時(shí)會(huì)造成燃燒機(jī)頻繁啟動(dòng)、加熱時(shí)間延長(zhǎng),造成不必要的天然氣浪費(fèi)。 3.2、爐門關(guān)閉不嚴(yán)。 爐門關(guān)閉不嚴(yán)同樣會(huì)造成爐內(nèi)能量的泄漏,增大天然氣消耗。
3.3、燃燒機(jī)燃燒效率低。 燃燒機(jī)燃燒時(shí),天然氣和助燃風(fēng)混合比例不合適,是造成燃燒機(jī)效率低的主要原因。天然氣比例過小時(shí)燃燒機(jī)容易熄火,天然氣比例大時(shí),天然氣燃燒不充分,未燃燒的天然氣會(huì)通過排煙系統(tǒng)排出爐外,這樣就會(huì)造成天然氣的白白浪費(fèi),同時(shí)升溫效果差。所以天然氣和助燃風(fēng)混合比例調(diào)整合適是減少天然氣消耗的主要方法。燃燒機(jī)火焰長(zhǎng)度一般以剛好出燒嘴口為宜,火焰形狀為“毛筆”形,火焰根部應(yīng)從槍口噴出,不能“脫火”,火焰顏色分里外兩層,中間為淡藍(lán)色,外層為淡紅色,火焰應(yīng)強(qiáng)勁有力。
3.4、天然氣質(zhì)量差、熱值低。 天然氣各組成成分主要包括辛烷、三甲基戊烷、甲苯、甲烷、已烷、丁烷等30多種成分。其中也包括二氧化碳、氣態(tài)水、空氣及一些惰性氣體。天然氣質(zhì)量差會(huì)使天然氣發(fā)熱量降低,直接造成天然氣能耗的增加。
3.5、排煙系統(tǒng)沒有經(jīng)過二次利用,直接排出爐外。 對(duì)煙氣進(jìn)行二次利用可以有效提高能量利用率,減少能源消耗。
3.6、一次裝爐量過小、兩次裝爐時(shí)間間隔太長(zhǎng),時(shí)效爐整體利用率低。 時(shí)效爐裝爐量過低時(shí)應(yīng)適當(dāng)縮短保溫時(shí)間,保溫時(shí)間的選擇應(yīng)根據(jù)鋁型材的壁厚和裝料的緊密程度來確定。這樣既可以滿足時(shí)效工藝,也可以有效降低天然氣及電能的消耗。兩次裝爐間隔時(shí)間過長(zhǎng)時(shí),爐內(nèi)溫度已降低很多,開始時(shí)效時(shí)爐壁就會(huì)吸收一些熱量以達(dá)到熱平衡,造成天然氣能耗的增加。
3.7、循環(huán)風(fēng)機(jī)轉(zhuǎn)速設(shè)置不合理。 我公司時(shí)效爐循環(huán)風(fēng)機(jī)的功率為75KW ,采用變頻器控制。我們知道電機(jī)的輸出功率和轉(zhuǎn)速的三次方成正比,即P∝n3。在滿足工藝的前提下,如果電機(jī)轉(zhuǎn)速設(shè)置過高就會(huì)造成電能的不必要浪費(fèi)。因此,合理設(shè)置風(fēng)機(jī)轉(zhuǎn)速是減少電能損耗的有效措施。 時(shí)效爐能耗高的原因很多,各單位應(yīng)根據(jù)時(shí)效爐的具體情況進(jìn)行分析,采取有效措施,在滿足時(shí)效工藝的前提下,盡可能降低天然氣和電能消耗。
4、時(shí)效過程中風(fēng)機(jī)轉(zhuǎn)速不合理的后果
鋁材時(shí)效過程一般分為升溫和保溫兩個(gè)階段,保溫時(shí)間比升溫時(shí)間一般要長(zhǎng)。在升溫階
段,為了滿足快速升溫的要求,風(fēng)機(jī)轉(zhuǎn)速較高,以加快熱空氣對(duì)流速度,滿足鋁型材從常溫升到180度左右溫度,當(dāng)然不同型號(hào)的鋁型材升溫溫度有所不同。在保溫階段,隨著時(shí)間的延長(zhǎng),鋁型材各部分已充分被加熱,爐內(nèi)熱空氣溫度和鋁型材溫度已基本達(dá)到熱平衡,這時(shí)熱空氣的對(duì)流速度已不需要太快,否則,不合理的風(fēng)機(jī)轉(zhuǎn)速使熱空氣對(duì)流速度迅速增大,爐內(nèi)溫度迅速上升在短時(shí)間內(nèi)超出保溫溫度,多余的熱量會(huì)通過煙道排除爐外,這樣不僅造成天然氣的浪費(fèi)而且風(fēng)機(jī)轉(zhuǎn)速高會(huì)造成風(fēng)機(jī)電能消耗大,最終造成時(shí)效成本增高。所以對(duì)大功率時(shí)效爐風(fēng)機(jī)轉(zhuǎn)速的合理設(shè)置意義重大。
5、本次技改主要研究?jī)?nèi)容和實(shí)施步驟。
5.1、對(duì)我公司時(shí)效爐能耗高的主要原因進(jìn)行客觀分析。
5.2、通過對(duì)時(shí)效爐鋁型材時(shí)效工藝的研究,理論確定升溫和保溫階段風(fēng)機(jī)運(yùn)行的最佳轉(zhuǎn)速,達(dá)到減少天然氣和電能的不必要損耗。 5.3、對(duì)廠家PLC程序中關(guān)于風(fēng)機(jī)控制子程序進(jìn)行分析,確定程序的不合理之處。
5.4、修改PLC風(fēng)機(jī)控制程序和變頻器參數(shù),并根據(jù)對(duì)時(shí)效爐溫升曲線多次在線測(cè)量和時(shí)效后樣品抗拉強(qiáng)度測(cè)定,計(jì)算并調(diào)整風(fēng)機(jī)轉(zhuǎn)速控制程序。 5.5、技改后,觀察時(shí)效用電單耗和天然氣單耗,得出節(jié)能降耗結(jié)果。
6、我公司時(shí)效爐能耗高的主要原因及解決方案
通過對(duì)第三項(xiàng)所列時(shí)效爐能耗高的主要原因進(jìn)行對(duì)照,結(jié)合我公司時(shí)效爐的具體情況進(jìn)行分析、查找,我公司時(shí)效爐能耗高的主要原因及解決方案論述如下:
6.1、兩次時(shí)效間隔時(shí)間過長(zhǎng),時(shí)效爐連續(xù)利用率低。 針對(duì)此問題,我們主要通過合理安排時(shí)效爐開爐時(shí)間,盡量保證鋁材時(shí)效量,盡可能縮短兩爐之間間隔時(shí)間,保持時(shí)效爐運(yùn)行的連續(xù)性。
6.2、在時(shí)效過程中循環(huán)風(fēng)機(jī)轉(zhuǎn)速設(shè)置不合理。 從技改前時(shí)效爐溫升曲線圖可以看出,在保溫階段,風(fēng)機(jī)轉(zhuǎn)速持續(xù)在50HZ以上顯然不合理。這樣高的轉(zhuǎn)速不僅增大了電能消耗而且溫升曲線在保溫段波動(dòng)較大,同時(shí)也增大了燃?xì)庀摹? 由n=60f/P*(1-s)可知,電機(jī)的轉(zhuǎn)速與頻率成正比,通過改變風(fēng)機(jī)電機(jī)的運(yùn)行頻率即改變了電機(jī)的轉(zhuǎn)速。 通過第四項(xiàng)的分析,結(jié)合我公司鋁型材時(shí)效的具體情況,經(jīng)過反復(fù)試驗(yàn),以TT板為例,我們將風(fēng)機(jī)頻率控制分為三個(gè)階段,在升溫階段通過PLC模擬量輸出模塊將變頻器的頻率控制在50HZ,進(jìn)入保溫段后的2小時(shí)30分內(nèi)的頻率控制在45.03HZ,其余時(shí)間設(shè)定為40HZ。修改程序后,完全能夠滿足時(shí)效工藝要求。同時(shí)由于變頻器輸出頻率比技改前降低,所以風(fēng)機(jī)消耗電功率也隨之降低。 當(dāng)然,由于每個(gè)廠家時(shí)效爐結(jié)構(gòu)及工藝要求的不同,對(duì)時(shí)效過程中風(fēng)機(jī)轉(zhuǎn)速的控制不能一概而論,應(yīng)結(jié)合時(shí)效鋁型材的具體牌號(hào)、升溫和保溫時(shí)間等因素通過實(shí)驗(yàn)手段進(jìn)行確定。
7、技改后時(shí)效效果及經(jīng)濟(jì)效益分析
通過對(duì)鋁型材時(shí)效爐時(shí)效工藝和設(shè)備現(xiàn)狀的研究、分析,找出能耗高的主要原因, 理論確定升溫和保溫階段風(fēng)機(jī)運(yùn)行的最佳轉(zhuǎn)速,在不改變?cè)O(shè)備現(xiàn)狀的前提下,通過修改PLC程序,既充分滿足時(shí)效工藝及時(shí)效效果而且有效降低了鋁型材時(shí)效過程中天然氣和電能的消耗,達(dá)到良好的節(jié)能效果。
7.1、時(shí)效爐技改前后的天然氣和用電單耗對(duì)比。 我公司在技改前,鋁材時(shí)效用電單耗為36KWh/T。技改后,鋁型材時(shí)效電單耗為25.8KWh/T ,技改后平均每噸電單耗下降10KWh左右。 技改前,時(shí)效爐天然氣平均單耗約為10.3m3 /T。技改后,時(shí)效爐天然氣平均單耗為10.6 m3/T,技改后天然氣平均單耗下降了0.7 m3 /T。
7.2、技改費(fèi)用: 由于本次技改是通過對(duì)時(shí)效過程中控制程序和變頻器的修改并通過測(cè)溫來達(dá)到節(jié)能效果,所以本次技改無直接費(fèi)用。
為了響應(yīng)國家節(jié)能減排號(hào)召,進(jìn)一步降低公司生產(chǎn)成本,保持設(shè)備安全、優(yōu)質(zhì)、經(jīng) 濟(jì)運(yùn)行。針對(duì)我公司A5、A6兩臺(tái)時(shí)效爐在運(yùn)行中存在溫升曲線差、電耗和天然氣消耗過大等問題,對(duì)時(shí)效爐能耗高的具體原因進(jìn)行分析并進(jìn)行節(jié)能降耗改造意義重大。時(shí)效爐能耗高的原因有很多,本文通過對(duì)我公司時(shí)效爐能耗高的主要原因進(jìn)行分析,對(duì)時(shí)效爐在升溫和保溫階段,循環(huán)風(fēng)機(jī)的最佳轉(zhuǎn)速控制進(jìn)行深入研究,通過修改PLC程序和變頻器參數(shù),合理控制風(fēng)機(jī)轉(zhuǎn)速,達(dá)到節(jié)約能耗目的。
1、鋁型材時(shí)效爐用途及結(jié)構(gòu)簡(jiǎn)介。
1.1、設(shè)備用途。
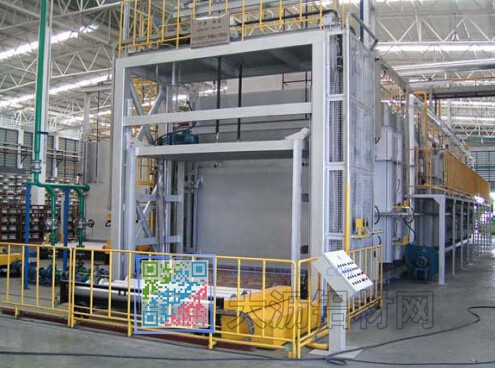
鋁合金時(shí)效爐主要用于鋁合金型材的時(shí)效處理。通過時(shí)效處理,可以使鋁合金強(qiáng)度和硬度大幅度提高,同時(shí)可以減少鋁合金材料的應(yīng)力集中、變形等問題。
1.2、時(shí)效爐結(jié)構(gòu)簡(jiǎn)介。 我公司時(shí)效爐主要由保溫爐體、爐門裝置、加熱系統(tǒng)、熱風(fēng)循環(huán)系統(tǒng)、臺(tái)車裝置及電氣控制系統(tǒng)等部分組成。 加熱系統(tǒng)采用1臺(tái)瑞典百通BG600燃?xì)馊紵龣C(jī),燃料為壓縮天然氣。為確保爐溫均勻性,爐體頂部設(shè)75KW離心式循環(huán)風(fēng)機(jī)1臺(tái),并合理配置爐內(nèi)熱風(fēng)循環(huán)導(dǎo)流系統(tǒng),使?fàn)t內(nèi)氣流分配均勻,爐內(nèi)溫差小,又保證了加熱速度與加熱質(zhì)量。爐體采用內(nèi)外兩層鋼板焊接而成的全金屬形結(jié)構(gòu),中間均勻填充硅酸鋁耐火纖維保溫,降低爐壁溫升。爐門采用電動(dòng)式升降爐門,爐門壓緊采用氣動(dòng)聯(lián)桿式四點(diǎn)平衡壓緊機(jī)構(gòu)。臺(tái)車牽引機(jī)構(gòu)采用鏈條式。
1.3、溫控系統(tǒng) 由觸摸屏、S7-200PLC、四支熱電偶、8通道無紙溫度記錄儀組成。升溫溫度、保溫溫度、升溫時(shí)間、保溫時(shí)間可分別在觸摸屏上進(jìn)行設(shè)置。 溫度控制采用級(jí)聯(lián)控制方式,即由4支溫度熱電偶采集的時(shí)效爐內(nèi)溫度信號(hào)送入PLC的閉環(huán)控制模塊經(jīng)冷端補(bǔ)償,線性化處理,與觸摸屏給定值一起經(jīng)運(yùn)算,其結(jié)果與爐溫度熱電偶采集的溫度信號(hào),再經(jīng)PLC運(yùn)算處理后,輸出給燃?xì)馊紵龣C(jī),從而控制火焰大小,達(dá)到溫度自動(dòng)調(diào)節(jié)的目的。同時(shí)通過PLC程序控制模擬量輸出模塊,輸出DC0-10V模擬量至變頻器,變頻器輸出相應(yīng)的頻率來控制循環(huán)風(fēng)機(jī)的轉(zhuǎn)速,以改變爐內(nèi)空氣的對(duì)流速度,使?fàn)t內(nèi)空氣溫度達(dá)到均勻化,完成鋁型材時(shí)效的目的。
2、興發(fā)鋁業(yè)技改前時(shí)效爐設(shè)備的現(xiàn)狀:
興發(fā)鋁業(yè)擠壓車間A5、A6時(shí)效爐均由某公司制造,加熱系統(tǒng)均采用1臺(tái)BG600天然氣燃燒機(jī),目前我公司主要時(shí)效的型材為6061和6082,升溫時(shí)間一般設(shè)定為1小時(shí)左右,保溫時(shí)間一般設(shè)定為6.5-7.5小時(shí)。每臺(tái)時(shí)效爐主要用電設(shè)備為75KW三相異步通風(fēng)機(jī)1臺(tái),采用PLC+變頻器自動(dòng)控制風(fēng)機(jī)的轉(zhuǎn)速,廠家設(shè)計(jì)的風(fēng)機(jī)轉(zhuǎn)速控制程序?yàn)樵陲L(fēng)機(jī)換向時(shí)程序輸出的頻率為52.9HZ,不換向時(shí)輸出頻率為57.02HZ。平均每噸鋁材時(shí)效耗電量為36KWh/噸。 天然氣平均耗氣量為10.3 m3 /噸。 我們通過多次溫度在線測(cè)量(參考7.4項(xiàng)升溫曲線圖),發(fā)現(xiàn)在升溫階段各部位溫差較大,在保溫階段曲線不夠平直,證明該時(shí)效爐溫度控制效果不理想。
3、時(shí)效爐能耗高的一般原因分析
由時(shí)效爐的結(jié)構(gòu)可以看出,時(shí)效爐的能源消耗主要包括由于加熱所產(chǎn)生的天然氣消耗和75KW循環(huán)風(fēng)機(jī)產(chǎn)生的電能消耗。
導(dǎo)致能耗高的可能原因分析如下:
3.1、時(shí)效爐爐體保溫效果差。 當(dāng)爐體保溫效果差時(shí),會(huì)使?fàn)t內(nèi)熱空氣通過熱傳導(dǎo)輻射到爐周圍空氣中,這勢(shì)必會(huì)造成升溫速度慢,不能滿足時(shí)效爐時(shí)效前期快速升溫的要求,同時(shí)會(huì)造成燃燒機(jī)頻繁啟動(dòng)、加熱時(shí)間延長(zhǎng),造成不必要的天然氣浪費(fèi)。 3.2、爐門關(guān)閉不嚴(yán)。 爐門關(guān)閉不嚴(yán)同樣會(huì)造成爐內(nèi)能量的泄漏,增大天然氣消耗。
3.3、燃燒機(jī)燃燒效率低。 燃燒機(jī)燃燒時(shí),天然氣和助燃風(fēng)混合比例不合適,是造成燃燒機(jī)效率低的主要原因。天然氣比例過小時(shí)燃燒機(jī)容易熄火,天然氣比例大時(shí),天然氣燃燒不充分,未燃燒的天然氣會(huì)通過排煙系統(tǒng)排出爐外,這樣就會(huì)造成天然氣的白白浪費(fèi),同時(shí)升溫效果差。所以天然氣和助燃風(fēng)混合比例調(diào)整合適是減少天然氣消耗的主要方法。燃燒機(jī)火焰長(zhǎng)度一般以剛好出燒嘴口為宜,火焰形狀為“毛筆”形,火焰根部應(yīng)從槍口噴出,不能“脫火”,火焰顏色分里外兩層,中間為淡藍(lán)色,外層為淡紅色,火焰應(yīng)強(qiáng)勁有力。
3.4、天然氣質(zhì)量差、熱值低。 天然氣各組成成分主要包括辛烷、三甲基戊烷、甲苯、甲烷、已烷、丁烷等30多種成分。其中也包括二氧化碳、氣態(tài)水、空氣及一些惰性氣體。天然氣質(zhì)量差會(huì)使天然氣發(fā)熱量降低,直接造成天然氣能耗的增加。
3.5、排煙系統(tǒng)沒有經(jīng)過二次利用,直接排出爐外。 對(duì)煙氣進(jìn)行二次利用可以有效提高能量利用率,減少能源消耗。
3.6、一次裝爐量過小、兩次裝爐時(shí)間間隔太長(zhǎng),時(shí)效爐整體利用率低。 時(shí)效爐裝爐量過低時(shí)應(yīng)適當(dāng)縮短保溫時(shí)間,保溫時(shí)間的選擇應(yīng)根據(jù)鋁型材的壁厚和裝料的緊密程度來確定。這樣既可以滿足時(shí)效工藝,也可以有效降低天然氣及電能的消耗。兩次裝爐間隔時(shí)間過長(zhǎng)時(shí),爐內(nèi)溫度已降低很多,開始時(shí)效時(shí)爐壁就會(huì)吸收一些熱量以達(dá)到熱平衡,造成天然氣能耗的增加。
3.7、循環(huán)風(fēng)機(jī)轉(zhuǎn)速設(shè)置不合理。 我公司時(shí)效爐循環(huán)風(fēng)機(jī)的功率為75KW ,采用變頻器控制。我們知道電機(jī)的輸出功率和轉(zhuǎn)速的三次方成正比,即P∝n3。在滿足工藝的前提下,如果電機(jī)轉(zhuǎn)速設(shè)置過高就會(huì)造成電能的不必要浪費(fèi)。因此,合理設(shè)置風(fēng)機(jī)轉(zhuǎn)速是減少電能損耗的有效措施。 時(shí)效爐能耗高的原因很多,各單位應(yīng)根據(jù)時(shí)效爐的具體情況進(jìn)行分析,采取有效措施,在滿足時(shí)效工藝的前提下,盡可能降低天然氣和電能消耗。
4、時(shí)效過程中風(fēng)機(jī)轉(zhuǎn)速不合理的后果
鋁材時(shí)效過程一般分為升溫和保溫兩個(gè)階段,保溫時(shí)間比升溫時(shí)間一般要長(zhǎng)。在升溫階
段,為了滿足快速升溫的要求,風(fēng)機(jī)轉(zhuǎn)速較高,以加快熱空氣對(duì)流速度,滿足鋁型材從常溫升到180度左右溫度,當(dāng)然不同型號(hào)的鋁型材升溫溫度有所不同。在保溫階段,隨著時(shí)間的延長(zhǎng),鋁型材各部分已充分被加熱,爐內(nèi)熱空氣溫度和鋁型材溫度已基本達(dá)到熱平衡,這時(shí)熱空氣的對(duì)流速度已不需要太快,否則,不合理的風(fēng)機(jī)轉(zhuǎn)速使熱空氣對(duì)流速度迅速增大,爐內(nèi)溫度迅速上升在短時(shí)間內(nèi)超出保溫溫度,多余的熱量會(huì)通過煙道排除爐外,這樣不僅造成天然氣的浪費(fèi)而且風(fēng)機(jī)轉(zhuǎn)速高會(huì)造成風(fēng)機(jī)電能消耗大,最終造成時(shí)效成本增高。所以對(duì)大功率時(shí)效爐風(fēng)機(jī)轉(zhuǎn)速的合理設(shè)置意義重大。
5、本次技改主要研究?jī)?nèi)容和實(shí)施步驟。
5.1、對(duì)我公司時(shí)效爐能耗高的主要原因進(jìn)行客觀分析。
5.2、通過對(duì)時(shí)效爐鋁型材時(shí)效工藝的研究,理論確定升溫和保溫階段風(fēng)機(jī)運(yùn)行的最佳轉(zhuǎn)速,達(dá)到減少天然氣和電能的不必要損耗。 5.3、對(duì)廠家PLC程序中關(guān)于風(fēng)機(jī)控制子程序進(jìn)行分析,確定程序的不合理之處。
5.4、修改PLC風(fēng)機(jī)控制程序和變頻器參數(shù),并根據(jù)對(duì)時(shí)效爐溫升曲線多次在線測(cè)量和時(shí)效后樣品抗拉強(qiáng)度測(cè)定,計(jì)算并調(diào)整風(fēng)機(jī)轉(zhuǎn)速控制程序。 5.5、技改后,觀察時(shí)效用電單耗和天然氣單耗,得出節(jié)能降耗結(jié)果。
6、我公司時(shí)效爐能耗高的主要原因及解決方案
通過對(duì)第三項(xiàng)所列時(shí)效爐能耗高的主要原因進(jìn)行對(duì)照,結(jié)合我公司時(shí)效爐的具體情況進(jìn)行分析、查找,我公司時(shí)效爐能耗高的主要原因及解決方案論述如下:
6.1、兩次時(shí)效間隔時(shí)間過長(zhǎng),時(shí)效爐連續(xù)利用率低。 針對(duì)此問題,我們主要通過合理安排時(shí)效爐開爐時(shí)間,盡量保證鋁材時(shí)效量,盡可能縮短兩爐之間間隔時(shí)間,保持時(shí)效爐運(yùn)行的連續(xù)性。
6.2、在時(shí)效過程中循環(huán)風(fēng)機(jī)轉(zhuǎn)速設(shè)置不合理。 從技改前時(shí)效爐溫升曲線圖可以看出,在保溫階段,風(fēng)機(jī)轉(zhuǎn)速持續(xù)在50HZ以上顯然不合理。這樣高的轉(zhuǎn)速不僅增大了電能消耗而且溫升曲線在保溫段波動(dòng)較大,同時(shí)也增大了燃?xì)庀摹? 由n=60f/P*(1-s)可知,電機(jī)的轉(zhuǎn)速與頻率成正比,通過改變風(fēng)機(jī)電機(jī)的運(yùn)行頻率即改變了電機(jī)的轉(zhuǎn)速。 通過第四項(xiàng)的分析,結(jié)合我公司鋁型材時(shí)效的具體情況,經(jīng)過反復(fù)試驗(yàn),以TT板為例,我們將風(fēng)機(jī)頻率控制分為三個(gè)階段,在升溫階段通過PLC模擬量輸出模塊將變頻器的頻率控制在50HZ,進(jìn)入保溫段后的2小時(shí)30分內(nèi)的頻率控制在45.03HZ,其余時(shí)間設(shè)定為40HZ。修改程序后,完全能夠滿足時(shí)效工藝要求。同時(shí)由于變頻器輸出頻率比技改前降低,所以風(fēng)機(jī)消耗電功率也隨之降低。 當(dāng)然,由于每個(gè)廠家時(shí)效爐結(jié)構(gòu)及工藝要求的不同,對(duì)時(shí)效過程中風(fēng)機(jī)轉(zhuǎn)速的控制不能一概而論,應(yīng)結(jié)合時(shí)效鋁型材的具體牌號(hào)、升溫和保溫時(shí)間等因素通過實(shí)驗(yàn)手段進(jìn)行確定。
7、技改后時(shí)效效果及經(jīng)濟(jì)效益分析
通過對(duì)鋁型材時(shí)效爐時(shí)效工藝和設(shè)備現(xiàn)狀的研究、分析,找出能耗高的主要原因, 理論確定升溫和保溫階段風(fēng)機(jī)運(yùn)行的最佳轉(zhuǎn)速,在不改變?cè)O(shè)備現(xiàn)狀的前提下,通過修改PLC程序,既充分滿足時(shí)效工藝及時(shí)效效果而且有效降低了鋁型材時(shí)效過程中天然氣和電能的消耗,達(dá)到良好的節(jié)能效果。
7.1、時(shí)效爐技改前后的天然氣和用電單耗對(duì)比。 我公司在技改前,鋁材時(shí)效用電單耗為36KWh/T。技改后,鋁型材時(shí)效電單耗為25.8KWh/T ,技改后平均每噸電單耗下降10KWh左右。 技改前,時(shí)效爐天然氣平均單耗約為10.3m3 /T。技改后,時(shí)效爐天然氣平均單耗為10.6 m3/T,技改后天然氣平均單耗下降了0.7 m3 /T。
7.2、技改費(fèi)用: 由于本次技改是通過對(duì)時(shí)效過程中控制程序和變頻器的修改并通過測(cè)溫來達(dá)到節(jié)能效果,所以本次技改無直接費(fèi)用。