1)定義以石油焦、瀝青焦或無煙煤為主要骨料,以煤瀝青等作粘結(jié)劑制成的糊類或塊類炭素制品,主要供金屬鋁電解生產(chǎn)過程中用作陰極和陽極,鎂冶煉、鐵合金生產(chǎn),一些化工窯爐有時也使用這些炭素材料。
2)作用鋁用炭素材料是鋁電解工業(yè)的支柱材料之一,主要作用為:用作電解槽的陽極,把電流導(dǎo)入電解槽,并參與電化學(xué)反應(yīng);用作電解槽的陰極內(nèi)襯,盛裝鋁液和電解質(zhì),并把電流導(dǎo)出電解槽外。
3)分類根據(jù)在電解槽中的位置和作用不同,可分為陽極材料和陰極材料兩大類(包括糊類和塊類制品)
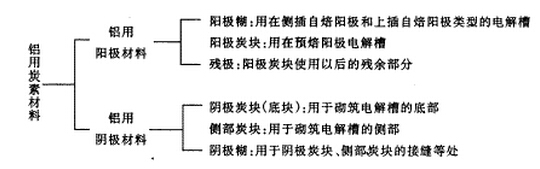
4)鋁電解工業(yè)采用炭素材料的歷史電解法制鋁的發(fā)明和每一次大的技術(shù)進步都是和炭素材料的發(fā)明和技術(shù)發(fā)展分不開的。19世紀(jì)70年代,已能生產(chǎn)炭質(zhì)電極和炭質(zhì)耐腐蝕材料。1888年,美國人霍爾(Hall.C.M)和法國人埃魯(Heroult.P.L.T)分別申請了冰晶石-氧化鋁熔鹽體系以炭電極為陽極、以石墨坩堝為容器和陰極,電解生產(chǎn)金屬鋁的專利。這種工業(yè)煉鋁方法,簡稱霍爾-埃魯法,到20世紀(jì)90年代,仍是唯一可以適于大規(guī)模工業(yè)生產(chǎn)金屬鋁的方法。由于冰晶石-氧化鋁體系具有強烈的腐蝕作用,要求電解槽的陽極和陰極材料具有耐高溫、導(dǎo)電性能良好、抗腐蝕、雜質(zhì)少等性能,一百多年的科學(xué)試驗和生產(chǎn)實踐表明,炭素材料是唯一能選作陽極和陰極的廉價的工業(yè)材料。
5)炭素材料石墨常用于鋁材擠壓潤滑劑,保護鋁型材,另外石墨具有良好的導(dǎo)電性,其導(dǎo)熱性能也比一般的非金屬材料和部分金屬材料好,致密石墨的抗壓強度也達到一定水平,因此石墨常用做發(fā)熱和成型材料,這樣的材料正好可用于制做熱壓燒結(jié)模具,用于生產(chǎn)金剛石刀頭。石墨做為模具材料也存在一定的不足,主要是氣孔率較大(相對金屬材料而言),熱壓時液態(tài)金屬有可能被擠入孔隙中,使模具變脆易開裂,并與模具粘連,影響使用壽命。這也是為什么要使用高強致密石墨和脫模劑的原因。
鋁電解生產(chǎn)初期采用小型預(yù)焙陽極。1887~1888年間,美國匹茲堡Reduction公司(ALCOA公司的前身)、瑞士冶金公司(AIAG和Aluoaisse的前身)依據(jù)霍爾—埃魯法,分別興建鋁電解槽,當(dāng)時的電流為1300~1800A。這種槽,陽極橫截面積小(8~10cm2),電流密度高(2~4A/cm2),陽極消耗量大(約2kg陽極/kg-A),電流效率低(50%~80%)。這種陽極用擠壓生產(chǎn)。由于當(dāng)時炭素技術(shù)不高,陽極質(zhì)量差,規(guī)格小,使電解槽的容量受到限制。
20世紀(jì)20年代,按照當(dāng)時鐵合金爐上連續(xù)自焙電極形式,在鋁電解槽上使用了連續(xù)自焙陽極,陽極導(dǎo)電棒采用側(cè)插式(1924年,挪威的S6derber9研制成功連續(xù)自焙陽極)。這種槽型在世界范圍推廣使用,陽極由圓形改為矩形,面積逐漸擴大,電解槽容量隨之提高,側(cè)插槽容量可達60kA以上。為了提高操作機械化程度和進—步擴大電解槽容量,l934年法國彼施涅鋁業(yè)公司(Pechiney)研制成功上插自焙陽極,隨后又實現(xiàn)多功能天車進行陽極操作。上插陽極的發(fā)展,使單槽電流容量達100~150kA以上。20世紀(jì)80年代,新型自焙陽極電解槽以炭素材料為主體構(gòu)成的自焙陽極,每個重達60~100k9,噸鋁消耗陽極糊降至600k9以下。自焙陽極使用過程中產(chǎn)生大量有害氣體,且不利于實現(xiàn)機械化、自動化。
圖1 炭素材料在鋁電解槽應(yīng)用結(jié)構(gòu)示意圖
a—預(yù)焙陽極電解槽(中部打殼);b—預(yù)焙陽極電解槽(邊部打殼);c—側(cè)插自焙陽極電解槽;d—上插自焙陽極電解槽
20世紀(jì)50年代,由于炭素電極技術(shù)的提高以及振動成型制造大規(guī)格預(yù)焙陽極炭塊的成功,由預(yù)焙陽極炭塊組裝而成預(yù)焙陽極電解槽被廣泛采用。80年代后期世界最新式的預(yù)焙陽極電解槽,預(yù)焙陽極由40余塊陽極炭塊組成,整個陽極重達50余噸,電解槽電流容量已達230kA以上。大型預(yù)焙陽極電解槽的電流效率可達93%以上,噸鋁消耗陽極炭塊降至500k9以下。由于預(yù)焙陽極煉鋁電解槽容量大,電耗低,環(huán)保好,1990年之后逐漸取代自焙陽極。
炭素材料生產(chǎn)技術(shù)的發(fā)展促進了鋁電解工業(yè)的發(fā)展,從而使鋁電解工業(yè)成為炭素制品的最大消費部門。圖2顯示了世界原鋁生產(chǎn)量的增長和炭陽極消耗量的增長。
中國在1990年以前,大多數(shù)中小電解鋁廠采用側(cè)插自焙陽極(30~60kA電解槽)和上插自焙陽極(80~100kA電解槽),大型電解鋁廠多采用預(yù)焙陽極(75kA、135kA、140kA、155kA、160kA電解槽),中國280kA預(yù)焙陽極的鋁電解槽于l995年工業(yè)試驗成功,1996年之后大型預(yù)焙陽極電解槽得到廣泛推廣。
圖2 1888年以來,世界原鋁生產(chǎn)增長和炭陽極消耗量
對鋁用炭素制品的質(zhì)量要求 炭素材料在鋁電解槽中參與導(dǎo)電和電化學(xué)反應(yīng),并直接與具有強腐蝕性的氟化物熔鹽接觸。因而,鋁電解工業(yè)對炭素材料提出如下要求:
(1)電阻率低。電阻率低有利于降低電能消耗。炭塊電阻率—般小于60μΩ•m,炭糊焙燒體電阻率—般小于80μΩ•m。
(2)體積密度大。較高的體積密度有利于抵抗熔鹽的侵蝕、降低氣體滲透、減少與CO2和空氣的反應(yīng)消耗。炭塊體積密度—般不小于1.559/cm3,炭糊焙燒體的體積密度不小于1.359/cm3。
(3)機械強度高。以炭素材料為主體構(gòu)成的電解槽陽極重達幾十噸,在電、熱沖擊下承重負荷。因此其機械強度要求比—般的炭素材料要高。炭塊的耐壓強度約為25-35MPa,炭糊焙燒體的耐壓強度約為18~28MPa。
(4)真密度高。陽極材料的真密度約為2.03~2.08g/cm3,陰極材料的真密度為1.84~1.909/cm3。
(5)雜質(zhì)含量低。陽極材料消耗以后,其中的雜質(zhì)直接進入電解質(zhì)和金屬鋁中,因此,要求陽極材料的雜質(zhì)含量低,—般不超過1%;陰極材料的雜質(zhì)含量—般不超過10%。
(6)與CO2氣體的反應(yīng)性能,炭素材料在950℃左右的高溫下使用,處于電解反應(yīng)所產(chǎn)生的CO2氣體包圍之中,因此,抵抗CO2氣體滲透和降低其反應(yīng)性,成為鋁用炭素材料的—項特殊性能要求。鋁用炭素材料CO2反應(yīng)性能指標(biāo)為:
1)總消耗率:炭塊類小于40mg/(cm2•h);炭糊類小于60mg/(cm2•h);
2)氣化率:炭塊類小于20%;炭糊類小于30%;
3)脫落度:炭塊類小于10%;炭糊類小于15%。
(7)電解膨脹率低。陰極材料長期受到電解質(zhì)的化學(xué)腐蝕而被破壞,電解膨脹率(或破損系數(shù))表示陰極材料在電解過程中抵抗電解質(zhì)腐蝕的能力。陰極材料的電解膨脹率小于1.4%,破損系數(shù)小于1.5。
中國鋁用炭素工業(yè)概況 中國鋁用炭素工業(yè)是與鋁工業(yè)相伴發(fā)展起來的。中華人民共和國建立之前,中國沒有單獨的鋁工業(yè)和鋁用炭素工業(yè)。在臺灣高雄和東北的撫順,日本人開辦的兩個小鋁廠設(shè)有陽極糊車間。20世紀(jì)50年代,中國第—家鋁廠——撫順鋁廠,第—家炭素廠——吉林炭素廠建有陽極糊和陰極炭塊生產(chǎn)線。20世紀(jì)50年代以來,中國相繼建立的撫順、山東、包頭、鄭州、青銅峽、貴州、蘭州、青海等10萬t以上大鋁廠多建有鋁用陽極材料生產(chǎn)線,1970年以前,各大鋁廠主要生產(chǎn)和使用陽極糊,幾十家地方鋁廠,自己不設(shè)陽極生產(chǎn),所用陽極從各炭素廠購進。1970年以后,中國自行研制成功預(yù)焙陽極炭塊制造技術(shù)和預(yù)焙陽極電解槽技術(shù);80年代初,從國外引進了先進的預(yù)焙陽極炭塊制造及預(yù)焙陽極電解槽技術(shù),這使中國鋁電解工業(yè)和鋁用炭素工業(yè)獲得巨大發(fā)展。特別在1996年之后,預(yù)焙陽極生產(chǎn)和預(yù)焙槽煉鋁發(fā)展很快。貴州、撫順、包頭、鄭州、白銀、青海平果、云南、焦作萬方、永城神火、運城關(guān)鋁、河南龍泉、永安鋁廠;山東荏平,南山等大鋁廠都全部采用預(yù)焙陽極煉鋁,從而大大促進了預(yù)焙陽極,炭塊的生產(chǎn)使原來弱小的鋁用炭素工業(yè)迅猛發(fā)展,到2000年中國有鋁用陽極生產(chǎn)廠家80家以上,總產(chǎn)量150多萬噸(表1)。
表1 中國鋁錠產(chǎn)量和陽極產(chǎn)品消耗量(萬t)
年代 |
1960 |
1970 |
1980 |
1990 |
1995 |
1998 |
2001 |
鋁錠產(chǎn)量 |
12 |
24 |
40 |
87 |
168 |
243 |
342 |
20世紀(jì)80年代以前,中國鋁用陰極制品主要由吉林炭素廠、蘭州炭素廠、上海炭素廠等供應(yīng)的普通陰極炭塊及糊類。80年代初,貴州鋁廠從日本引進了半石墨陰極炭塊及陰極糊類生產(chǎn)線,促進了中國陰極生產(chǎn)技術(shù)的發(fā)展。山西炭素廠是中國最早的陰極制品的專業(yè)生產(chǎn)廠家。
20世紀(jì)80年代,中國為鋁電解服務(wù)的有幾十家中小炭素廠,它們主要生產(chǎn)陽極糊、陰極炭塊、側(cè)部炭塊等。l992年,中國鋁用炭素制品生產(chǎn)能力約66萬t/a。1996年之后,隨著鋁工業(yè)的迅猛發(fā)展,鋁用炭素工業(yè)迅速興起(表2)。
表2 2001年中國主要鋁用炭素廠生產(chǎn)廠家及產(chǎn)能(萬t)
廠家 |
陽極產(chǎn)品 |
陰極產(chǎn)品 |
廠家 |
陽極產(chǎn)品 |
陰極產(chǎn)品 |
廠家 |
陽極產(chǎn)品 |
陰極產(chǎn)品 |
貴州鋁廠 |
13 |
2.0 |
包頭鋁廠 |
7 |
|
山東鋁廠 |
4 |
|
焦作萬方 |
6 |
|
|
|
|
|
|
|
中國鋁用炭素材料的科研進展 鋁用炭素材料的質(zhì)量對鋁電解生產(chǎn)的電流效率、直流電耗和生產(chǎn)成本影響很大。1984年,中國有色金屬工業(yè)總公司成立后,提出“優(yōu)先發(fā)展鋁”的方針,十分重視鋁用炭素的科技發(fā)展。1985年成立了以鄭州輕金屬研究院為組長單位的鋁用炭素科技協(xié)作網(wǎng),把“提高鋁用炭素材料質(zhì)量”列為國家“七五”科技攻關(guān)項目,撥100多萬元專款在鄭州輕金屬研究院建立鋁用炭素研究室和鋁用炭素質(zhì)檢中心,為全國鋁行業(yè)和鋁用炭素行業(yè)服務(wù)。1985年以來,中國科研、設(shè)計、生產(chǎn)幾十家單位聯(lián)合攻關(guān),已先后研制成功了半石墨陰極炭塊、干陽極糊、添加劑陽極糊、SiC側(cè)部炭塊、氮化硅結(jié)合碳化硅側(cè)塊、硼化鈦復(fù)合炭塊冷搗糊、冷搗糊、大顆粒配方、改質(zhì)瀝青、多工位振動成型機等新產(chǎn)品、新技術(shù)、新裝備;并先后開發(fā)了—系列鋁用炭素專用的檢測設(shè)備,如陰極材料電解膨脹率測定儀、陽極材料c02反應(yīng)性測定儀(圖3)等。