孫東立 姜石峰 高興錫
摘 要:采用光學顯微鏡,掃描電子顯微鏡,透射電子顯微鏡,電子探針X射線微區(qū)分析儀和定量圖像分析儀研究了3004鋁合金鑄態(tài)和均勻化退火態(tài)的顯微組織以及均勻化退火溫度和時間對顯微組織的影響。在鑄態(tài)組織中發(fā)現(xiàn)了一種新的富MgSiCu的共晶體。在均勻化退火過程中發(fā)生β→α相變和α彌散相的脫溶析出。在試驗條件下,最佳均勻化退火工藝為615℃,20h。經此工藝處理可獲得較均勻的顯微組織。
關鍵詞:Al-Mn-Mg合金;均勻化退火;顯微組織
Key words: Al-Mn-Mg alloys; homogenizing annealing; microstructure
在過去20年間,3XXX系鋁合金一直被用作飲料罐體材料,世界各國對該系合金進行了大量的研究[1~6]。目前對此類罐體合金的需求量在逐年增長,預計在未來相當長的時間內這種增長趨勢不會減弱[7]。鋁罐的制造工藝包括合金鑄造,鑄錠均勻化退火,熱軋,再結晶退火和最終冷軋。其中均勻化退火是最關鍵的工藝。因為均勻化退火后的顯微組織決定了后續(xù)工藝的組織狀態(tài),進而影響鋁罐的最終性能。本文研究了當前大量使用的罐體材料——3004合金的鑄態(tài)和均勻化退火態(tài)的顯微組織,并著重研究了均勻化退火工藝對第二相粒子的影響以及均勻化過程中發(fā)生的α相變。 1 試驗材料及方法 試驗合金的化學成分是(massfraction,%):1.20Mn,1.10Mg,0.28Si,0.48Fe,0.20Cu,其余為Al。鑄錠在空氣爐內進行均勻化退火,然后淬入室溫水中。退火溫度分別為595℃和615℃,退火時間為5,10和20h,加熱速率為5℃/min。
采用光學顯微鏡(OM),JSM-5800型掃描電子顯微鏡(SEM)和JEOL-2000透射電子顯微鏡(TEM)進行顯微組織觀察。金相試樣采用混合酸腐蝕。第二相粒子的成分用JXA-8600型電子探針X射線微區(qū)分析儀(EPMA)測定。第二相粒子的體積分數(面積百分數)和尺寸用LECO-2000型圖像分析系統(tǒng)測定。用于成分分析和定量圖像分析的試樣只拋光不腐蝕。 2 試驗結果與分析 2.1 鑄態(tài)顯微組織
圖1示出了鑄錠的光學顯微組織。由圖可見,鑄態(tài)組織是不均勻的,主要由樹枝狀的α-Al相和枝晶間的共晶體組成,共晶體中含有粗大的金屬間化合物粒子,這些粒子呈骨骼狀、塊狀和片狀。EPMA成分分析結果表明,大部分金屬間化合物粒子是Al6(FeMn)相,少量的是Mg2Si相。Mg2Si相為細小的黑色骨骼狀粒子(見圖1(a))。在晶界附近或者枝晶臂之間,甚至在共晶α-Al內部存在許多細小的第二相粒子(見圖1(c))。在透射電鏡下可以看到,這些粒子為針狀,并且沿著基體〈100〉α-Al方向生長(見圖2)。因此可以推斷這些針狀相是Mg2Si相,該相是在合金凝固之后鑄錠冷卻期間從固溶體中析出的,共晶α-Al中Mg2Si相存在可以證實這一點。
圖1 在鑄態(tài)組織中發(fā)現(xiàn)一種圓形(或橢圓形)粒子。在高放大倍數下可見該粒子為兩相層片相間的共晶體(見圖1(b))。該共晶體的直徑約為4~10μm,其中的兩種片狀共晶相的片間距小于EPMA的束斑直徑(2μm),無法分別測定它們各自的成分,只能測出該共晶體的平均成分。EPMA的半定量測量結果表明,該共晶體含有(molefraction,%):15.03Mg,14.18Si,4.68Cu,<0.55(Mn+Fe)和65.57Al。這種富MgSiCu的共晶體尚未見有文獻報道。有關該共晶體的特性和其對合金性能的影響有待進一步的研究。
在3XXX系合金的鑄態(tài)組織中通常存在兩種主要的初生第二相粒子——β-Al6(FeMn)和α-Al12(FeMn)3Si,兩種粒子的相對含量取決于具體的合金成分和凝固速率[8]。在本試驗所采用的鑄錠中,僅檢測到少量(體積分數小于10%)的初生α-Al12(FeMn)3Si粒子。兩種初生第二相粒子的形貌無顯著差別。
圖2 2.2 均勻化態(tài)的顯微組織
圖3顯示了均勻化態(tài)的光學顯微組織。均勻化處理使骨骼狀、塊狀和片狀粒子球化,使針狀Mg2Si相溶解,同時在晶內析出細小的彌散相。595℃均勻化處理后第二相粒子的球化不完全,彌散相分布亦不均勻,即在晶界和粗大第二相粒子附近存在彌散相無析出帶。此無析出帶形成的原因是Mn在晶內偏聚和在含Mn第二相粒子內部的富集所導致的上述區(qū)域Mn的貧化[9]。在較高的均勻化溫度(615℃)下原子擴散速率較快,因而第二相粒子充分球化,且彌散相無析出帶較窄,第二相粒子和彌散相分布較為均勻。延長加熱時間同提高均勻化溫度有著類似的作用,但是前者的作用小于后者。光學顯微組織的觀察結果表明,本試驗所采用的均勻化退火工藝中,615℃加熱20h是較好的工藝。
圖3 均勻化退火態(tài)的光學顯微組織
Fig.3 Optical microstructure in homogenized state
(a)—595℃, 20h; (b)—615℃, 5h; (c)—615℃, 20h 2.3 均勻化處理對初生第二相粒子幾何特征的影響
表1列出了鑄態(tài)和均勻化退火態(tài)初生第二相粒子的體積分數和平均尺寸。鑄錠中的初生第二相粒子的體積分數為4.1%。595℃均勻化退火對初生第二相粒子的體積分數影響甚微,但是初生第二相粒子的尺寸和縱橫比小于鑄態(tài),并且隨著加熱時間由5h延長至20h,初生第二相粒子的平均尺寸和縱橫比分別由17.3μm2和2.29減小至14.4μm2和1.95。615℃均勻化退火使初生第二相粒子的體積分數減少至3.5%~3.6%。第二相粒子的平均尺寸和縱橫比分別減小至10.1~10.6μm2和1.81~1.50。以上試驗結果表明,在本試驗條件下均勻化退火溫度對初生第二相粒子的影響大于加熱時間。在較高的溫度下,原子擴散速率快,促進了初生第二相粒子的球化。另外溫度高有利于不平衡共晶體和不平衡相的溶解,從而導致初生第二相粒子體積分數的減少。 表1 均勻化退火對初生第二相粒子幾何特征的影響
Table 1 Effect of homogenization on primary second particle geometry鑄態(tài)組織中的針狀Mg2Si相
Fig.2 Needle-like Mg2Si phase in ingot 鑄錠的光學顯微組織
Fig.1 Optical microstructure of ingot
(a)(b)—non-etched; (c)—etched
2.4 均勻化退火過程中的相變
圖4示出均勻化退火態(tài)初生第二相粒子形貌。由圖可見,部分初生第二相粒子含有亮點。經電子探針測定,這些粒子的成分為Al12-(FeMn)3Si,即為α相[10~13];而亮點區(qū)域Si,F(xiàn)e和Mn的含量較低,Al的含量相對較高,故將亮點區(qū)稱為Al點[14]。含有Al點為α-Al12-(FeMn)3Si粒子的形貌特征。不含有Al點的初生第二相粒子經電子探針測定,其成分為Al6(FeMn),即為β相。
圖4 α相為立方結構,其點陣常數為1.255~1.265nm[15~17]。圖5(a)中的粒子尺寸約為3 μm×6.3μm,并有亮點。通過計算該粒子的選區(qū)電子衍射斑點,可知該粒子的點陣結構為立方結構,點陣常數約為1.263nm。因此可以確定圖5(a)中的粒子是在均勻化退火過程中
由初生β粒子轉變而成的α粒子。初步的定量分析結果顯示,595℃和615℃退火20h后由β相轉變生成的α相所占的體積分別為75%和40%左右。此結果表明β→α轉變具有最佳溫度。α相的硬度高于β相,在鋁罐成型過程中可防止鋁罐與模具之間的摩擦,提高罐體表面的光潔度[18]。α相的體積分數和尺寸對性能的影響還有待進一步的研究。
圖5 退火后針狀的Mg2Si相消失了,取而代之的是一些尺寸小于0.2μm的塊狀粒子,如圖6(b)所示。該圖中粒子的微衍射斑點花樣與α相相符。因而可以認定這些細小粒子是在均勻化退火期間從基體中析出的。加熱溫度超過500℃時Mg2Si相溶解,使基體中Si含量增高。一部分Si通過擴散進入初生β相,促進了β相向α相的轉變;另一部分Si參與脫溶析出,形成α彌散相。 3 結論 (1)在鑄態(tài)合金中發(fā)現(xiàn)了一種新的富MgSiCu的共晶體。
(2)均勻化退火溫度的升高和時間的延長,使初生金屬間化合物粒子的體積分數略有減少,但粒子的縱橫比和平均尺寸明顯減??;初生第二相和彌散析出相分布的均勻性增大。在本試驗條件下,最佳均勻化退火工藝為615℃/20h。
(3)在均勻化退火過程中部分初生β-Al6(FeMn)轉變成α-Al12(FeMn)3Si相,同時從過飽和固溶體中析出α-Al12(FeMn)3Si彌散相。 作者單位:孫東立(1.哈爾濱工業(yè)大學材料科學與工程學院,哈爾濱150001;
姜石峰 高興錫2.韓國機械材料研究院,昌原641-010,韓國)
摘 要:采用光學顯微鏡,掃描電子顯微鏡,透射電子顯微鏡,電子探針X射線微區(qū)分析儀和定量圖像分析儀研究了3004鋁合金鑄態(tài)和均勻化退火態(tài)的顯微組織以及均勻化退火溫度和時間對顯微組織的影響。在鑄態(tài)組織中發(fā)現(xiàn)了一種新的富MgSiCu的共晶體。在均勻化退火過程中發(fā)生β→α相變和α彌散相的脫溶析出。在試驗條件下,最佳均勻化退火工藝為615℃,20h。經此工藝處理可獲得較均勻的顯微組織。
關鍵詞:Al-Mn-Mg合金;均勻化退火;顯微組織
Key words: Al-Mn-Mg alloys; homogenizing annealing; microstructure
在過去20年間,3XXX系鋁合金一直被用作飲料罐體材料,世界各國對該系合金進行了大量的研究[1~6]。目前對此類罐體合金的需求量在逐年增長,預計在未來相當長的時間內這種增長趨勢不會減弱[7]。鋁罐的制造工藝包括合金鑄造,鑄錠均勻化退火,熱軋,再結晶退火和最終冷軋。其中均勻化退火是最關鍵的工藝。因為均勻化退火后的顯微組織決定了后續(xù)工藝的組織狀態(tài),進而影響鋁罐的最終性能。本文研究了當前大量使用的罐體材料——3004合金的鑄態(tài)和均勻化退火態(tài)的顯微組織,并著重研究了均勻化退火工藝對第二相粒子的影響以及均勻化過程中發(fā)生的α相變。 1 試驗材料及方法 試驗合金的化學成分是(massfraction,%):1.20Mn,1.10Mg,0.28Si,0.48Fe,0.20Cu,其余為Al。鑄錠在空氣爐內進行均勻化退火,然后淬入室溫水中。退火溫度分別為595℃和615℃,退火時間為5,10和20h,加熱速率為5℃/min。
采用光學顯微鏡(OM),JSM-5800型掃描電子顯微鏡(SEM)和JEOL-2000透射電子顯微鏡(TEM)進行顯微組織觀察。金相試樣采用混合酸腐蝕。第二相粒子的成分用JXA-8600型電子探針X射線微區(qū)分析儀(EPMA)測定。第二相粒子的體積分數(面積百分數)和尺寸用LECO-2000型圖像分析系統(tǒng)測定。用于成分分析和定量圖像分析的試樣只拋光不腐蝕。 2 試驗結果與分析 2.1 鑄態(tài)顯微組織
圖1示出了鑄錠的光學顯微組織。由圖可見,鑄態(tài)組織是不均勻的,主要由樹枝狀的α-Al相和枝晶間的共晶體組成,共晶體中含有粗大的金屬間化合物粒子,這些粒子呈骨骼狀、塊狀和片狀。EPMA成分分析結果表明,大部分金屬間化合物粒子是Al6(FeMn)相,少量的是Mg2Si相。Mg2Si相為細小的黑色骨骼狀粒子(見圖1(a))。在晶界附近或者枝晶臂之間,甚至在共晶α-Al內部存在許多細小的第二相粒子(見圖1(c))。在透射電鏡下可以看到,這些粒子為針狀,并且沿著基體〈100〉α-Al方向生長(見圖2)。因此可以推斷這些針狀相是Mg2Si相,該相是在合金凝固之后鑄錠冷卻期間從固溶體中析出的,共晶α-Al中Mg2Si相存在可以證實這一點。
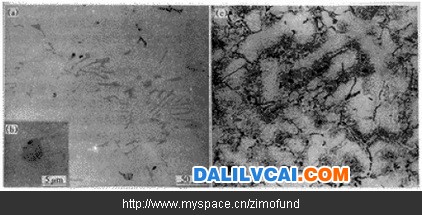
圖1 在鑄態(tài)組織中發(fā)現(xiàn)一種圓形(或橢圓形)粒子。在高放大倍數下可見該粒子為兩相層片相間的共晶體(見圖1(b))。該共晶體的直徑約為4~10μm,其中的兩種片狀共晶相的片間距小于EPMA的束斑直徑(2μm),無法分別測定它們各自的成分,只能測出該共晶體的平均成分。EPMA的半定量測量結果表明,該共晶體含有(molefraction,%):15.03Mg,14.18Si,4.68Cu,<0.55(Mn+Fe)和65.57Al。這種富MgSiCu的共晶體尚未見有文獻報道。有關該共晶體的特性和其對合金性能的影響有待進一步的研究。
在3XXX系合金的鑄態(tài)組織中通常存在兩種主要的初生第二相粒子——β-Al6(FeMn)和α-Al12(FeMn)3Si,兩種粒子的相對含量取決于具體的合金成分和凝固速率[8]。在本試驗所采用的鑄錠中,僅檢測到少量(體積分數小于10%)的初生α-Al12(FeMn)3Si粒子。兩種初生第二相粒子的形貌無顯著差別。
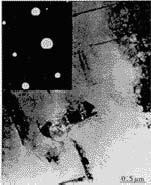
圖2 2.2 均勻化態(tài)的顯微組織
圖3顯示了均勻化態(tài)的光學顯微組織。均勻化處理使骨骼狀、塊狀和片狀粒子球化,使針狀Mg2Si相溶解,同時在晶內析出細小的彌散相。595℃均勻化處理后第二相粒子的球化不完全,彌散相分布亦不均勻,即在晶界和粗大第二相粒子附近存在彌散相無析出帶。此無析出帶形成的原因是Mn在晶內偏聚和在含Mn第二相粒子內部的富集所導致的上述區(qū)域Mn的貧化[9]。在較高的均勻化溫度(615℃)下原子擴散速率較快,因而第二相粒子充分球化,且彌散相無析出帶較窄,第二相粒子和彌散相分布較為均勻。延長加熱時間同提高均勻化溫度有著類似的作用,但是前者的作用小于后者。光學顯微組織的觀察結果表明,本試驗所采用的均勻化退火工藝中,615℃加熱20h是較好的工藝。
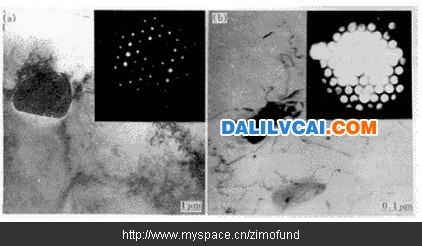
圖3 均勻化退火態(tài)的光學顯微組織
Fig.3 Optical microstructure in homogenized state
(a)—595℃, 20h; (b)—615℃, 5h; (c)—615℃, 20h 2.3 均勻化處理對初生第二相粒子幾何特征的影響
表1列出了鑄態(tài)和均勻化退火態(tài)初生第二相粒子的體積分數和平均尺寸。鑄錠中的初生第二相粒子的體積分數為4.1%。595℃均勻化退火對初生第二相粒子的體積分數影響甚微,但是初生第二相粒子的尺寸和縱橫比小于鑄態(tài),并且隨著加熱時間由5h延長至20h,初生第二相粒子的平均尺寸和縱橫比分別由17.3μm2和2.29減小至14.4μm2和1.95。615℃均勻化退火使初生第二相粒子的體積分數減少至3.5%~3.6%。第二相粒子的平均尺寸和縱橫比分別減小至10.1~10.6μm2和1.81~1.50。以上試驗結果表明,在本試驗條件下均勻化退火溫度對初生第二相粒子的影響大于加熱時間。在較高的溫度下,原子擴散速率快,促進了初生第二相粒子的球化。另外溫度高有利于不平衡共晶體和不平衡相的溶解,從而導致初生第二相粒子體積分數的減少。 表1 均勻化退火對初生第二相粒子幾何特征的影響
Table 1 Effect of homogenization on primary second particle geometry鑄態(tài)組織中的針狀Mg2Si相
Fig.2 Needle-like Mg2Si phase in ingot 鑄錠的光學顯微組織
Fig.1 Optical microstructure of ingot
(a)(b)—non-etched; (c)—etched
AlloystateArea | Area /μm2 |
Length /μm |
Width /μm |
Aspect ratio |
Volume fraction/% |
As-cast | 21.7 | 8.4 | 3.6 | 2.35 | 4.1 |
595℃,5h | 17.3 | 7.7 | 3.4 | 2.29 | 4.1 |
595℃,10h | 16.2 | 7.4 | 3.3 | 2.23 | 4.0 |
595℃,20h | 14.4 | 6.4 | 3.3 | 1.95 | 4.1 |
615℃,5h | 10.6 | 4.9 | 2.7 | 1.81 | 3.6 |
615℃,10h | 10.3 | 4.3 | 2.8 | 1.54 | 3.6 |
615℃,20h | 10.1 | 4.2 | 2.8 | 1.50 | 3.5 |
圖4示出均勻化退火態(tài)初生第二相粒子形貌。由圖可見,部分初生第二相粒子含有亮點。經電子探針測定,這些粒子的成分為Al12-(FeMn)3Si,即為α相[10~13];而亮點區(qū)域Si,F(xiàn)e和Mn的含量較低,Al的含量相對較高,故將亮點區(qū)稱為Al點[14]。含有Al點為α-Al12-(FeMn)3Si粒子的形貌特征。不含有Al點的初生第二相粒子經電子探針測定,其成分為Al6(FeMn),即為β相。
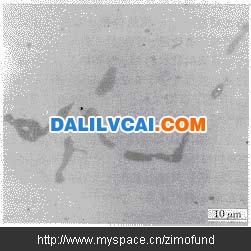
圖4 α相為立方結構,其點陣常數為1.255~1.265nm[15~17]。圖5(a)中的粒子尺寸約為3 μm×6.3μm,并有亮點。通過計算該粒子的選區(qū)電子衍射斑點,可知該粒子的點陣結構為立方結構,點陣常數約為1.263nm。因此可以確定圖5(a)中的粒子是在均勻化退火過程中
由初生β粒子轉變而成的α粒子。初步的定量分析結果顯示,595℃和615℃退火20h后由β相轉變生成的α相所占的體積分別為75%和40%左右。此結果表明β→α轉變具有最佳溫度。α相的硬度高于β相,在鋁罐成型過程中可防止鋁罐與模具之間的摩擦,提高罐體表面的光潔度[18]。α相的體積分數和尺寸對性能的影響還有待進一步的研究。
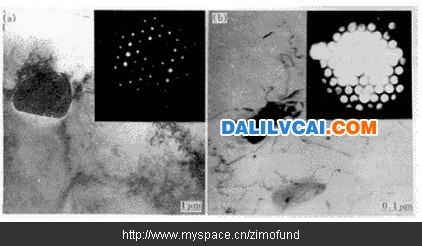
圖5 退火后針狀的Mg2Si相消失了,取而代之的是一些尺寸小于0.2μm的塊狀粒子,如圖6(b)所示。該圖中粒子的微衍射斑點花樣與α相相符。因而可以認定這些細小粒子是在均勻化退火期間從基體中析出的。加熱溫度超過500℃時Mg2Si相溶解,使基體中Si含量增高。一部分Si通過擴散進入初生β相,促進了β相向α相的轉變;另一部分Si參與脫溶析出,形成α彌散相。 3 結論 (1)在鑄態(tài)合金中發(fā)現(xiàn)了一種新的富MgSiCu的共晶體。
(2)均勻化退火溫度的升高和時間的延長,使初生金屬間化合物粒子的體積分數略有減少,但粒子的縱橫比和平均尺寸明顯減??;初生第二相和彌散析出相分布的均勻性增大。在本試驗條件下,最佳均勻化退火工藝為615℃/20h。
(3)在均勻化退火過程中部分初生β-Al6(FeMn)轉變成α-Al12(FeMn)3Si相,同時從過飽和固溶體中析出α-Al12(FeMn)3Si彌散相。 作者單位:孫東立(1.哈爾濱工業(yè)大學材料科學與工程學院,哈爾濱150001;
姜石峰 高興錫2.韓國機械材料研究院,昌原641-010,韓國)