激光填絲焊接鋁合金不但可以保持激光焊固有的優(yōu)點,如能量集中、變形小等,還可以降低對接焊時的間隙裕度,減少焊接缺陷,提高接頭性能等,從而擴大鋁合金薄板激光焊接在航空航天工業(yè)中的應(yīng)用。
鋁合金是航空航天工業(yè)中的主要結(jié)構(gòu)材料,它不僅具有高比強度、高比模量、良好的斷裂韌性、疲勞強度和較低的裂紋擴展速率,同時還具有優(yōu)良的成形工藝性和良好的耐蝕性。在民用飛機中,鋁合金占結(jié)構(gòu)材料重量百分比高達70%~80%。在新一代軍用飛機中,由于復(fù)合材料和鈦合金用量的增加,鋁合金的用量有所減少,但高純、高強、高韌的高性能鋁合金用量卻增加了。蘇-27飛機上鋁合金約占全機結(jié)構(gòu)重量的60%。
激光焊接具有能量集中、焊接變形小、焊縫質(zhì)量優(yōu)良、生產(chǎn)效率高等優(yōu)點,此外激光的柔性更增加了焊接工藝的靈活性。在飛機制造中,激光焊接可以實現(xiàn)飛機結(jié)構(gòu)以焊代鉚以及替代常規(guī)焊接方法提高焊縫質(zhì)量。因此對鋁合金的激光焊接技術(shù)研究成為各國特別是航空航天制造工業(yè)界的焦點。
1.焊接接頭的化學成份完全取決于母材,性能不能按要求進行調(diào)整;激光焊接鋁合金時,低沸點元素容易蒸發(fā)造成接頭性能下降。
2.激光焊接對接頭間隙要求嚴格,自熔焊所允許的間隙量最大不超過板厚的10%。在實際生產(chǎn)中,尤其對于航空航天工業(yè),不可避免地會遇到對薄板的對接激光焊,當薄板厚度為1.2mm或者更薄時,對接焊的間隙要求很難滿足。如果對薄板采用曲面對接焊,這一間隙要求更難達到。雖然通過機械加工可以使被焊工件的裝配間隙符合要求,但這勢必增加成本,更不利于激光焊接在工業(yè)生產(chǎn)中推廣應(yīng)用。
3.激光焊接鋁合金時過程不穩(wěn)定,焊縫成形不理想,且由于熔池中高反射率和低表面張力,將會導(dǎo)致焊縫缺陷,如焊塌、氣孔和軟化等。
采用激光填絲焊接技術(shù)(Laser Welding Technique with Filler Wire)不僅可以保持激光焊固有的優(yōu)點,還可以改善鋁合金激光焊接的表面成形,提高接頭的力學性能,防止裂紋產(chǎn)生,以較小的功率實現(xiàn)厚板的焊接等,從而大大擴展激光焊接的可能性與應(yīng)用范圍。因此,激光填絲焊接技術(shù)是激光焊接的發(fā)展與應(yīng)用中必須解決的一項基本技術(shù)。
激光填絲焊接的原理如圖1所示,該工藝與“掃描”加工方式不同的是,聚焦激光斑點不是直接照射在工件表面,而是照射到焊絲上,焊絲金屬熔化后再進入待焊兩工件之間,為了保護加工區(qū)和控制光致等離子體,還需要向激光束和焊絲及工件作用部位吹送保護氣體。為了實現(xiàn)單面焊雙面成形,保證焊縫背面成形,還必須對其施加背保護。
激光填絲焊裝置
在對鋁合金激光填絲焊接技術(shù)研究中,送絲直徑最小為0.8mm,配合機器人實現(xiàn)自動化焊接。由于鋁絲質(zhì)軟易卷曲,在送絲過程中易出現(xiàn)堆絲,因此送絲系統(tǒng)理想的驅(qū)動方式是推-拉絲方式,即在焊絲盤一端推,在焊接頭一端拉,如圖2所示。在推絲送絲方式的焊把上加裝了微型電動機作為拉絲動力。焊絲前進時既靠后邊的推力,又靠前邊的拉力,利用二者的合力來克服焊絲軟管中的阻力。一般來說,在推-拉絲式送絲方式中,推絲電動機是主要的送絲動力,它保證等速送進焊絲。拉絲電動機只起到隨時將焊絲拉直的作用。在推拉式送絲方式中,兩個動力要有一定的配合,盡量做到同步,但以推為主。在焊絲送進過程中,始終要保持焊絲在軟管中處于拉直狀態(tài)。這樣就要求拉絲動力稍快于推絲動力,這兩個動力之間要保持一定的速率比。
激光填絲焊成形控制
在激光焊接過程中,橫向于焊接方向的送絲位置偏差WY(見圖3)所引起的問題尤為突出。例如,對于WY=0.25mm的位置偏差,當采用?2填充焊絲時相對于直徑1.0焊絲熔化效率將下降30%;相對于直徑1.2焊絲熔化效率將下降36%。當位置偏差WY=0.4mm時,將造成嚴重不均勻的熔敷焊道。因此,WY應(yīng)盡量接近0mm。而試驗證明WX應(yīng)控制在0.3~2mm之間焊接效果最佳。
圖5為對接間隙約0.1mm,焊絲直徑1.2mm,焊接速度4.5m/min,激光功率3100W,焊縫成形最好的送絲速度約是5m/min。因此,對于某種材料的激光填絲焊接技術(shù),送絲速度的確定還具有不確定性。
最大間隙容許裕度指焊接過程中不能獲得良好焊縫成形的起始失效處的間隙寬度。通過對接變間隙法試驗證明,鋁合金激光填絲焊的最大間隙容許裕度較激光焊而言有顯著增加。例如,1.2mm厚的5A06鋁合金薄板的對接適應(yīng)間隙最大可以達到約1mm,如圖6所示。這明顯高于激光對接焊時最大容許間隙裕度(板厚的10﹪即0.12mm)。
對于1.2mm厚的5A06鋁合金激光填絲焊接焊縫,選取典型試件進行X光探傷試驗,X射線檢測未發(fā)現(xiàn)超標缺陷,達到HB5375-87Ⅰ級焊縫的技術(shù)要求。同時,焊接接頭的抗拉強度和屈服強度均達到母材水平。
1.多道填絲焊技術(shù)
采用多道焊技術(shù)可以提高激光焊接厚板的能力。例如焊前試板加工成階梯形坡口還是雙邊V型坡口,當選用匹配的工藝參數(shù),就能獲得較好的焊縫。確定合理的焊接順序,可以最大程度地減小焊接變形。同其他焊接方法相比,焊接坡口間隙很小,這有利于改善焊接質(zhì)量,節(jié)約焊接成本,提高生產(chǎn)效率。
2.異種金屬焊接
鋁合金是航空航天工業(yè)中的主要結(jié)構(gòu)材料,它不僅具有高比強度、高比模量、良好的斷裂韌性、疲勞強度和較低的裂紋擴展速率,同時還具有優(yōu)良的成形工藝性和良好的耐蝕性。在民用飛機中,鋁合金占結(jié)構(gòu)材料重量百分比高達70%~80%。在新一代軍用飛機中,由于復(fù)合材料和鈦合金用量的增加,鋁合金的用量有所減少,但高純、高強、高韌的高性能鋁合金用量卻增加了。蘇-27飛機上鋁合金約占全機結(jié)構(gòu)重量的60%。
激光焊接具有能量集中、焊接變形小、焊縫質(zhì)量優(yōu)良、生產(chǎn)效率高等優(yōu)點,此外激光的柔性更增加了焊接工藝的靈活性。在飛機制造中,激光焊接可以實現(xiàn)飛機結(jié)構(gòu)以焊代鉚以及替代常規(guī)焊接方法提高焊縫質(zhì)量。因此對鋁合金的激光焊接技術(shù)研究成為各國特別是航空航天制造工業(yè)界的焦點。
激光焊接如果不填絲,將存在如下局限性:
1.焊接接頭的化學成份完全取決于母材,性能不能按要求進行調(diào)整;激光焊接鋁合金時,低沸點元素容易蒸發(fā)造成接頭性能下降。
2.激光焊接對接頭間隙要求嚴格,自熔焊所允許的間隙量最大不超過板厚的10%。在實際生產(chǎn)中,尤其對于航空航天工業(yè),不可避免地會遇到對薄板的對接激光焊,當薄板厚度為1.2mm或者更薄時,對接焊的間隙要求很難滿足。如果對薄板采用曲面對接焊,這一間隙要求更難達到。雖然通過機械加工可以使被焊工件的裝配間隙符合要求,但這勢必增加成本,更不利于激光焊接在工業(yè)生產(chǎn)中推廣應(yīng)用。
3.激光焊接鋁合金時過程不穩(wěn)定,焊縫成形不理想,且由于熔池中高反射率和低表面張力,將會導(dǎo)致焊縫缺陷,如焊塌、氣孔和軟化等。
同時,鋁合金對氣孔有最大的敏感性,而氫是鋁及鋁合金熔焊時產(chǎn)生氣孔的主要原因。氫之所以能使焊縫形成氣孔,與其在鋁及鋁合金中溶解度的變化特性有關(guān)。平衡條件下,氫在鋁及鋁合金中的溶解度在凝固點時可以從0.69ml/100g突降到0.036ml/100g ,相差約20倍(在鋼中只相差不到2倍),這是氫容易使焊縫產(chǎn)生氣孔的重要原因之一。另外,鋁的導(dǎo)熱性很強,在同樣的工藝條件下,鋁熔合區(qū)的冷卻速度可為鋼的4~7倍,不利于氣泡的逸出,更易于促使氣孔形成。這些問題制約了激光焊接技術(shù)在航空航天及國防工業(yè)等領(lǐng)域的應(yīng)用。
采用激光填絲焊接技術(shù)(Laser Welding Technique with Filler Wire)不僅可以保持激光焊固有的優(yōu)點,還可以改善鋁合金激光焊接的表面成形,提高接頭的力學性能,防止裂紋產(chǎn)生,以較小的功率實現(xiàn)厚板的焊接等,從而大大擴展激光焊接的可能性與應(yīng)用范圍。因此,激光填絲焊接技術(shù)是激光焊接的發(fā)展與應(yīng)用中必須解決的一項基本技術(shù)。
激光填絲焊接的原理如圖1所示,該工藝與“掃描”加工方式不同的是,聚焦激光斑點不是直接照射在工件表面,而是照射到焊絲上,焊絲金屬熔化后再進入待焊兩工件之間,為了保護加工區(qū)和控制光致等離子體,還需要向激光束和焊絲及工件作用部位吹送保護氣體。為了實現(xiàn)單面焊雙面成形,保證焊縫背面成形,還必須對其施加背保護。
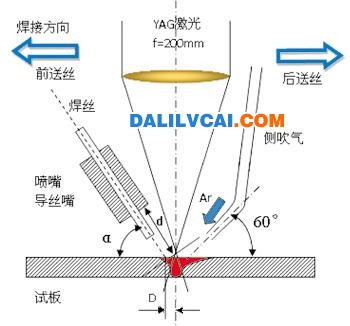
圖1 激光填絲焊接裝置示意圖
研究鋁合金薄板的激光填絲焊接性,為該技術(shù)在我國飛機制造和宇航服中的應(yīng)用打下基礎(chǔ)。同時,還可以解決型號研制中鋁合金激光焊接不能填絲這一“瓶頸”問題,為工程化應(yīng)用提供技術(shù)支持。
激光填絲焊裝置
在對鋁合金激光填絲焊接技術(shù)研究中,送絲直徑最小為0.8mm,配合機器人實現(xiàn)自動化焊接。由于鋁絲質(zhì)軟易卷曲,在送絲過程中易出現(xiàn)堆絲,因此送絲系統(tǒng)理想的驅(qū)動方式是推-拉絲方式,即在焊絲盤一端推,在焊接頭一端拉,如圖2所示。在推絲送絲方式的焊把上加裝了微型電動機作為拉絲動力。焊絲前進時既靠后邊的推力,又靠前邊的拉力,利用二者的合力來克服焊絲軟管中的阻力。一般來說,在推-拉絲式送絲方式中,推絲電動機是主要的送絲動力,它保證等速送進焊絲。拉絲電動機只起到隨時將焊絲拉直的作用。在推拉式送絲方式中,兩個動力要有一定的配合,盡量做到同步,但以推為主。在焊絲送進過程中,始終要保持焊絲在軟管中處于拉直狀態(tài)。這樣就要求拉絲動力稍快于推絲動力,這兩個動力之間要保持一定的速率比。
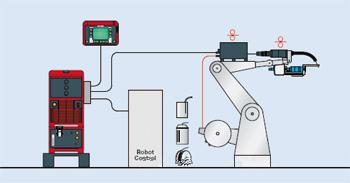
圖2 推-拉絲送絲方式
激光填絲焊成形控制
激光填絲焊接技術(shù)的關(guān)鍵是確定焊絲的送絲位置和送絲速度。送絲位置是指在焊接方向上相對于匙孔的位置偏差(Wx)以及沿激光束軸線橫穿匙孔的位置偏差(Wz),如圖3所示。送絲方式分為前送絲和后送絲。前送絲是指與焊接方向相反,焊絲末端指向匙孔前邊緣的送進方式;后送絲是指與焊接方向相同,焊絲末端指向匙孔后邊緣的送進方式。一般認為,前送絲方式可以使填充材料在焊縫中的分布更加均勻。
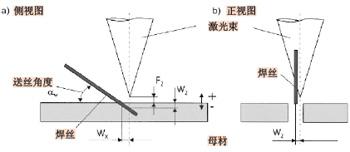
圖3 激光焊過程中填充焊絲相對于激光束、工件表面和接縫的參數(shù)圖
在激光焊接過程中,橫向于焊接方向的送絲位置偏差WY(見圖3)所引起的問題尤為突出。例如,對于WY=0.25mm的位置偏差,當采用?2填充焊絲時相對于直徑1.0焊絲熔化效率將下降30%;相對于直徑1.2焊絲熔化效率將下降36%。當位置偏差WY=0.4mm時,將造成嚴重不均勻的熔敷焊道。因此,WY應(yīng)盡量接近0mm。而試驗證明WX應(yīng)控制在0.3~2mm之間焊接效果最佳。
相對于工件表面的送絲角度αw由焊接裝置的幾何尺寸決定,通常在比較寬的范圍內(nèi)即30~75。金屬材料的反射率作為沖擊角的函數(shù)而變化。當該角接近90時反射率達到最低。但這個角度在實際中無法實現(xiàn)。試驗獲得該角度在50~60范圍內(nèi),能保證焊絲的最大穩(wěn)定性和焊縫的最好力學性能。
激光填絲焊接過程中送絲速度必須和焊接速度、激光功率等焊接工藝參數(shù)相匹配,過大的送絲速度將導(dǎo)致焊縫余高過大,而送絲速度太小則會產(chǎn)生不規(guī)則的焊縫成形。專家曾指出激光焊接過程中焊絲幾乎100%過渡到焊接熔池中,因此根據(jù)焊接過程的物質(zhì)平衡計算出送絲速度的預(yù)測公式。
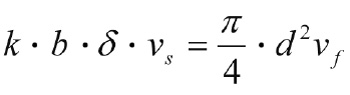
式中:b為拼縫間隙(mm);δ為工件厚度(mm);vs為焊接速度(m/min);d為焊絲直徑(mm);vf為送絲速度(m/min);k為成形系數(shù),成形系數(shù)由余高的要求確定,約為1.2~1.3。
通過試驗證明,該公式對于3mm厚鋁鋰合金的激光填絲焊基本符合,但是對于1.2mm厚的5A06鋁合金薄板并不符合。如圖4所示兩個空間曲面之間為堆焊時焊縫成形較好的送絲速度選擇范圍。
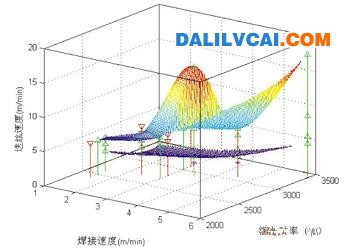
圖4 1.2mm厚5A06鋁合金薄板送絲速度選擇范圍
圖5為對接間隙約0.1mm,焊絲直徑1.2mm,焊接速度4.5m/min,激光功率3100W,焊縫成形最好的送絲速度約是5m/min。因此,對于某種材料的激光填絲焊接技術(shù),送絲速度的確定還具有不確定性。
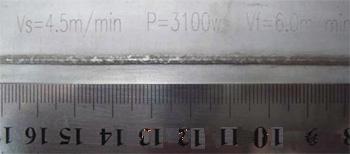
圖5 5A06鋁合金薄板激光填絲焊縫形貌
間隙適應(yīng)性及性能
最大間隙容許裕度指焊接過程中不能獲得良好焊縫成形的起始失效處的間隙寬度。通過對接變間隙法試驗證明,鋁合金激光填絲焊的最大間隙容許裕度較激光焊而言有顯著增加。例如,1.2mm厚的5A06鋁合金薄板的對接適應(yīng)間隙最大可以達到約1mm,如圖6所示。這明顯高于激光對接焊時最大容許間隙裕度(板厚的10﹪即0.12mm)。
對于1.2mm厚的5A06鋁合金激光填絲焊接焊縫,選取典型試件進行X光探傷試驗,X射線檢測未發(fā)現(xiàn)超標缺陷,達到HB5375-87Ⅰ級焊縫的技術(shù)要求。同時,焊接接頭的抗拉強度和屈服強度均達到母材水平。

圖6 間隙對激光填絲焊縫成形的影響
發(fā)展方向
1.多道填絲焊技術(shù)
采用多道焊技術(shù)可以提高激光焊接厚板的能力。例如焊前試板加工成階梯形坡口還是雙邊V型坡口,當選用匹配的工藝參數(shù),就能獲得較好的焊縫。確定合理的焊接順序,可以最大程度地減小焊接變形。同其他焊接方法相比,焊接坡口間隙很小,這有利于改善焊接質(zhì)量,節(jié)約焊接成本,提高生產(chǎn)效率。
2.異種金屬焊接
異種金屬焊接時,由于對接的基體金屬化學成分及組織有較大差異,因此采用自熔焊技術(shù)很難得到滿意的接頭質(zhì)量。但填絲焊卻可以彌補自熔焊的不足,通過選用合適的填充焊絲可以使焊接接頭具有優(yōu)良的綜合性能。
3.激光熱絲焊技術(shù)
當對焊絲未采用加熱措施時,激光束的能量有很大一部分作用在焊絲上,這無疑會降低焊接速度。為了充分利用激光束的能量優(yōu)勢,引入了熱絲焊工藝。熱絲焊減少了激光消耗在焊絲上的能量,從而提高了焊接速度。激光熱絲焊工藝需增加一套預(yù)熱設(shè)備,一般采用電阻加熱??芍苯訉㈦姌O接在送絲滾輪上,通過大電流將焊絲在瞬間加熱至接近熔點溫度,當焊絲被送到焊接熔池邊時,由于焊絲表面溫度很高,僅需很少的激光能量就能將其熔化。而熔化的焊絲能吸收大量的激光能量,并向母材傳導(dǎo)。同自熔焊相比,熱絲焊更有利于激光能量的吸收。因此,激光熱絲焊的焊接速度可以比自熔焊更高。
激光填絲焊由于能夠增加焊縫最大間隙裕度,改善接頭的組織和性能,增強焊接厚板及異種金屬能力,極大地擴展了激光焊接的應(yīng)用范圍。對激光填絲焊在航空航天材料中的進一步研究,可以推動航空航天制造技術(shù)的發(fā)展,加快對傳統(tǒng)工業(yè)的改造。因此,激光填絲焊的研究具有廣闊的前景。