建筑鋁型材靜電粉末涂裝技術是近年來迅速起來的一項表面處理技術,它的特點不含溶劑,不污染環(huán)境,粉末可以回收,容易實現(xiàn)自動化生產(chǎn),使用方便,而且涂層顏色多樣、可以滿足不同耐候性能要求。然而,在鋁型材靜電粉末噴涂中經(jīng)常出現(xiàn)一些缺陷,影響產(chǎn)品的外觀質量及使用性能。
以下將簡單介紹常見的涂層缺陷成因及控制措施:
一、缺陷名稱:顆粒
成因分析:基材表面有毛刺、鋁屑及石墨痕等,前處理不良;前處理槽液殘渣粘附在型材表面,水洗不凈到位;涂裝前鉻化料放置時間較長,表面吸附著粉塵;新燒掛具使用不當,導致鉻化料表面落灰;粉末、回收粉中可能含雜質;噴涂現(xiàn)場和固化爐不潔凈有懸浮物。
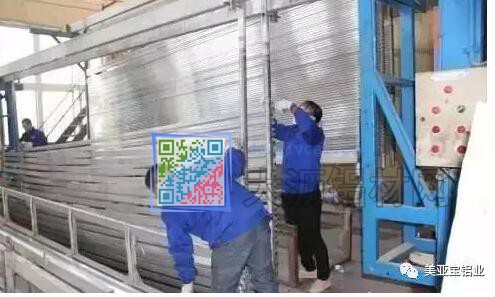
控制措施:上排前打磨好坯料表面或噴砂處理,確保前處理到位;定期倒槽,清理殘渣,延長純水洗時間;鉻化料上排后仔細吹塵;新燒掛具噴一層較薄涂膜后使用;回收粉宜過篩后使用;車間實行6S管理,保存噴涂現(xiàn)場整潔,定期清理固化爐。
二、缺陷名稱:露底
成因分析:粉末涂料的覆蓋力較差;型材斷面結構復雜容易造成靜電屏蔽效應;掛料方式不當;噴房工責任心不強,業(yè)務能力差,上粉膜厚判斷不當;噴槍口積粉太多,堵塞;噴槍移動速度太快或鏈速太快;型材裝飾面認識不清晰。
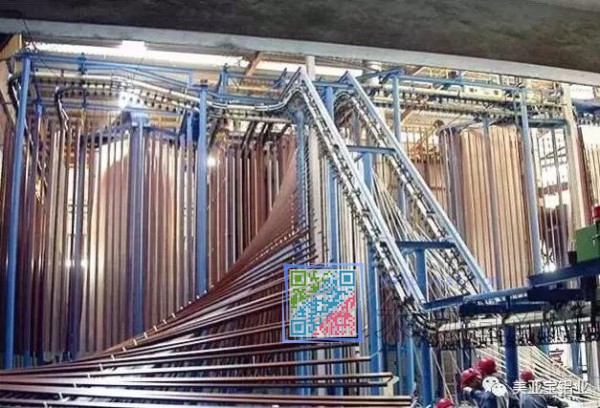
控制措施:嚴格控制粉末涂料質量;對型材凹槽、內角手動補粉;調整型材掛料角度;提高噴房工技能,噴房工盡量第一時間測量固化后型材膜厚;定期清理噴槍口,保持通暢;調整噴槍移動速度,適當降低鏈速;了解客戶噴涂要求,認清型材的裝飾面。
三、缺陷名稱:涂層不均
成因分析:鉻化料的懸掛方式和排列不當;型材接地不良(個別掛具導電不良);輸送鏈速度不均勻,或鏈速與噴槍升降速度不協(xié)調,型材裝飾面的粉末覆蓋次數(shù)不一致;噴槍的出粉量和粉末霧化不當;壓縮空氣壓力不穩(wěn)定;高電靜電發(fā)生器電壓不穩(wěn),靜電高壓變化。
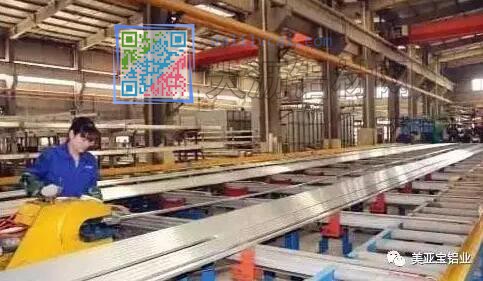
控制措施:加強噴房上排工與噴房工的溝通工作,做好型材對應掛具的選用;檢查掛具是否導電;噴房工加強機能提升,噴涂時做好掛料密度、鏈速與升降速度的協(xié)調;控制好抽粉氣和送粉氣比例;加強設備維護保養(yǎng),保持設備運行穩(wěn)定。
四、缺陷名稱:雜色
成因分析:噴房工在換色清理噴房的時候,清理不夠徹底而滲粉造成雜色;對粉末(回收粉)使用未及時烤板,校正顏色;噴房周圍環(huán)境不清潔。
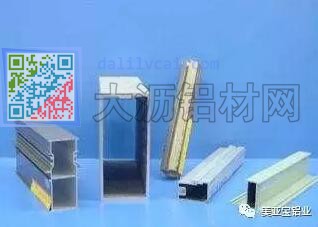
控制措施:噴房工在清理噴房時,要仔細清理每一細節(jié),尤其噴槍粉管徹底清理,大旋風要認真吹干凈,清理完噴房在涂裝前必須烤板確認是否有雜色;回收粉須烤板確認合格后使用,隨時保持噴房周邊衛(wèi)生清潔。
五、缺陷名稱:縮孔
成因分析:前處理脫脂不徹底;壓縮空氣質量不合格,供粉氣體和霧化氣體含有油分;鉻化料周轉過程中可能受到油污、水漬污染;鏈條下接油盤變形,造成鏈條滴油污染;樹脂不兼容,混粉而引起的縮孔。
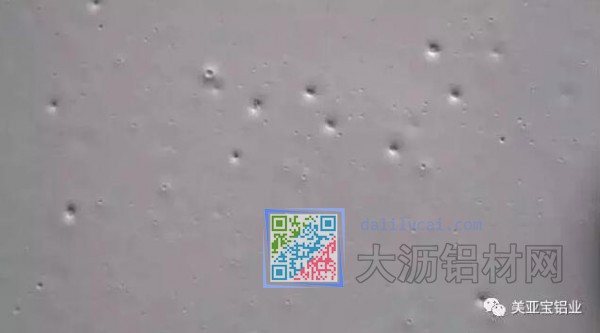
控制措施:調整脫脂工藝,保證型材除油干凈;仔細檢查鉻化料表面質量,存放及周轉鉻化料時防止油、水污染;檢查壓縮空氣質量和除水除油設備的運轉情況,及時排放壓縮空氣冷凝水及油;檢查鏈條潤滑油使用情況,避免造成污染;使用精細清理模式換色,清吹干凈粉管及噴粉系統(tǒng)。
六、缺陷名稱:粗砂
成因分析:粗砂是指砂紋粉末涂層表面較粗糙的現(xiàn)象,主要原因有:靜電噴涂時型材邊緣或尖端放電,電壓偏高;噴槍與型材距離偏小,電場強度過大;掛具導電不良導致上粉不好或反向電離嚴重;粉末質量較差造成固化后涂層粗糙。
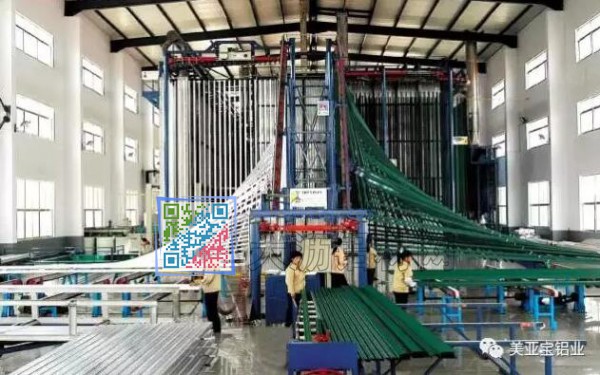
控制措施:嚴格控制靜電壓、噴槍與型材距離等,執(zhí)行噴粉工藝要求;掛料前,應將掛具與鏈條、型材之間的節(jié)點充分打磨以保證導電良好;嚴格控制粉末涂料質量。
七、缺陷名稱:色差
成因分析:粉末顏料不均勻引起色差;不同批次粉末涂料;固化溫度及時間不同;涂層膜厚不均勻。
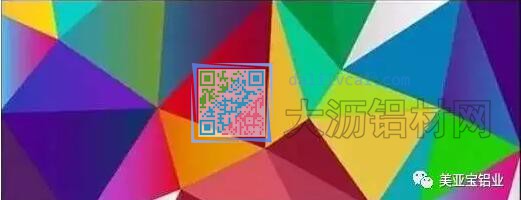
控制措施:加強粉末質量監(jiān)控;不同批次的粉末涂料,新粉入庫烤板檢驗;保持同一批噴涂型材固化溫度和時間一致,特殊粉末須固定生產(chǎn)線涂裝鋁材;加強噴粉工藝控制,避免涂層膜厚差距過大。
八、缺陷名稱:涂層擦劃傷
成因分析:噴涂成品下排、周轉、貼膜前,由于長短料相互摩擦,或人工操作不當,造成噴涂料裝飾面擦劃傷。
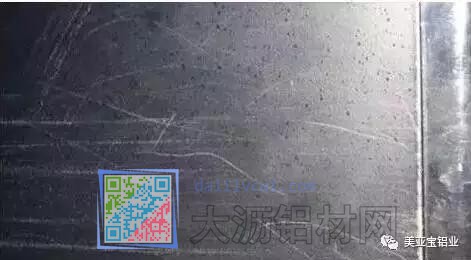
控制措施:將下排的噴涂成品按長度不同,分類放置;工人搬運型材時須相互配合,做到輕拿輕放。
九、缺陷名稱:吐粉
成因分析:粉末受潮結團而致流化效果差,輸粉管中粉末濃度不均勻;流化板被粉末堵塞,供粉裝置流化效果差;粉管、粉泵、文丘管、靜電針、噴槍嘴等配件上附著粉垢或磨損嚴重,導致出粉量不均勻,出現(xiàn)吐粉現(xiàn)象。
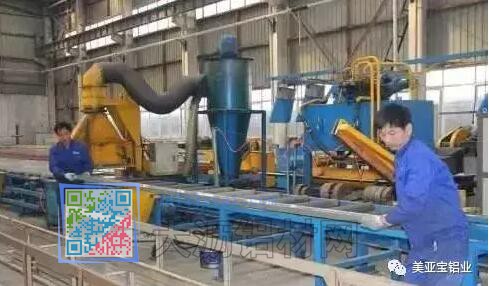
控制措施:改善粉末貯存環(huán)境,粉末使用后及時封箱避免粉末受潮;做好供粉設備維修保養(yǎng);及時清理噴房設備配件上的粉垢,并更換磨損配件。
在實際粉末噴涂生產(chǎn)中,須精細化管理每一道工序,針對出現(xiàn)的涂層缺陷對癥下藥,盡量避免重復出現(xiàn)類似涂層缺陷,這樣才能在降低生產(chǎn)成本的同時提高粉末涂裝質量。
以下將簡單介紹常見的涂層缺陷成因及控制措施:
一、缺陷名稱:顆粒
成因分析:基材表面有毛刺、鋁屑及石墨痕等,前處理不良;前處理槽液殘渣粘附在型材表面,水洗不凈到位;涂裝前鉻化料放置時間較長,表面吸附著粉塵;新燒掛具使用不當,導致鉻化料表面落灰;粉末、回收粉中可能含雜質;噴涂現(xiàn)場和固化爐不潔凈有懸浮物。
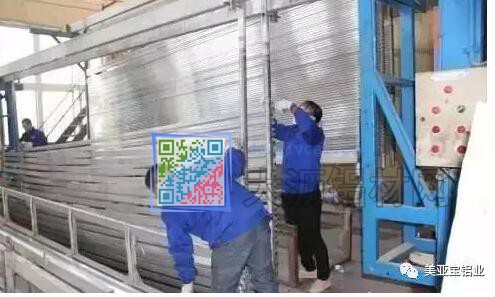
控制措施:上排前打磨好坯料表面或噴砂處理,確保前處理到位;定期倒槽,清理殘渣,延長純水洗時間;鉻化料上排后仔細吹塵;新燒掛具噴一層較薄涂膜后使用;回收粉宜過篩后使用;車間實行6S管理,保存噴涂現(xiàn)場整潔,定期清理固化爐。
二、缺陷名稱:露底
成因分析:粉末涂料的覆蓋力較差;型材斷面結構復雜容易造成靜電屏蔽效應;掛料方式不當;噴房工責任心不強,業(yè)務能力差,上粉膜厚判斷不當;噴槍口積粉太多,堵塞;噴槍移動速度太快或鏈速太快;型材裝飾面認識不清晰。
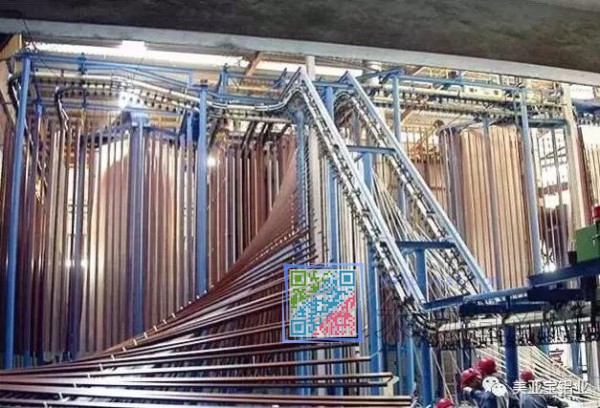
控制措施:嚴格控制粉末涂料質量;對型材凹槽、內角手動補粉;調整型材掛料角度;提高噴房工技能,噴房工盡量第一時間測量固化后型材膜厚;定期清理噴槍口,保持通暢;調整噴槍移動速度,適當降低鏈速;了解客戶噴涂要求,認清型材的裝飾面。
三、缺陷名稱:涂層不均
成因分析:鉻化料的懸掛方式和排列不當;型材接地不良(個別掛具導電不良);輸送鏈速度不均勻,或鏈速與噴槍升降速度不協(xié)調,型材裝飾面的粉末覆蓋次數(shù)不一致;噴槍的出粉量和粉末霧化不當;壓縮空氣壓力不穩(wěn)定;高電靜電發(fā)生器電壓不穩(wěn),靜電高壓變化。
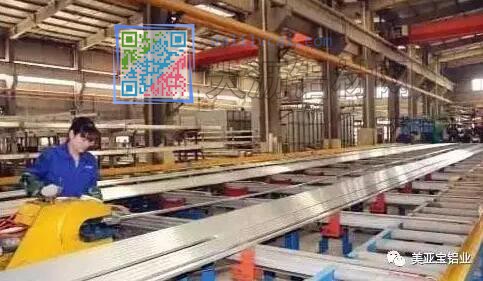
控制措施:加強噴房上排工與噴房工的溝通工作,做好型材對應掛具的選用;檢查掛具是否導電;噴房工加強機能提升,噴涂時做好掛料密度、鏈速與升降速度的協(xié)調;控制好抽粉氣和送粉氣比例;加強設備維護保養(yǎng),保持設備運行穩(wěn)定。
四、缺陷名稱:雜色
成因分析:噴房工在換色清理噴房的時候,清理不夠徹底而滲粉造成雜色;對粉末(回收粉)使用未及時烤板,校正顏色;噴房周圍環(huán)境不清潔。
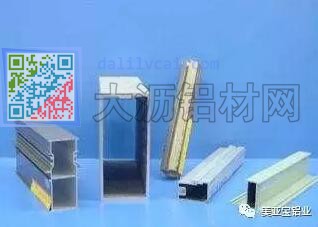
控制措施:噴房工在清理噴房時,要仔細清理每一細節(jié),尤其噴槍粉管徹底清理,大旋風要認真吹干凈,清理完噴房在涂裝前必須烤板確認是否有雜色;回收粉須烤板確認合格后使用,隨時保持噴房周邊衛(wèi)生清潔。
五、缺陷名稱:縮孔
成因分析:前處理脫脂不徹底;壓縮空氣質量不合格,供粉氣體和霧化氣體含有油分;鉻化料周轉過程中可能受到油污、水漬污染;鏈條下接油盤變形,造成鏈條滴油污染;樹脂不兼容,混粉而引起的縮孔。
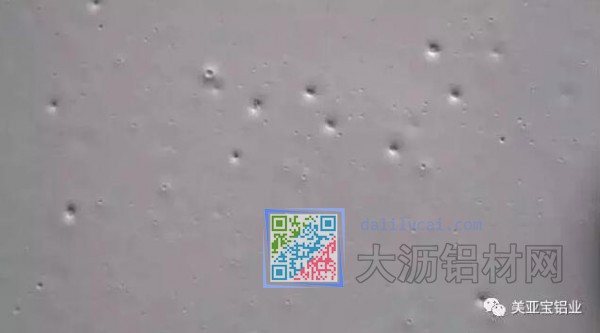
控制措施:調整脫脂工藝,保證型材除油干凈;仔細檢查鉻化料表面質量,存放及周轉鉻化料時防止油、水污染;檢查壓縮空氣質量和除水除油設備的運轉情況,及時排放壓縮空氣冷凝水及油;檢查鏈條潤滑油使用情況,避免造成污染;使用精細清理模式換色,清吹干凈粉管及噴粉系統(tǒng)。
六、缺陷名稱:粗砂
成因分析:粗砂是指砂紋粉末涂層表面較粗糙的現(xiàn)象,主要原因有:靜電噴涂時型材邊緣或尖端放電,電壓偏高;噴槍與型材距離偏小,電場強度過大;掛具導電不良導致上粉不好或反向電離嚴重;粉末質量較差造成固化后涂層粗糙。
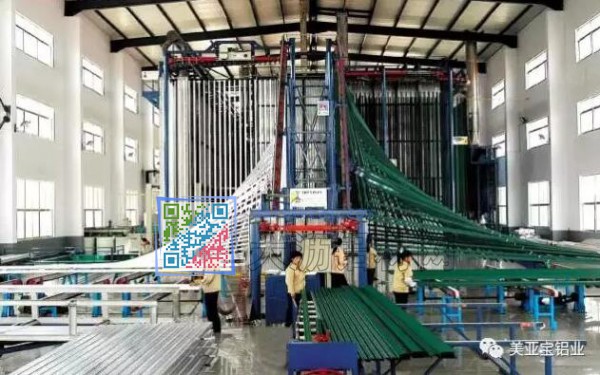
控制措施:嚴格控制靜電壓、噴槍與型材距離等,執(zhí)行噴粉工藝要求;掛料前,應將掛具與鏈條、型材之間的節(jié)點充分打磨以保證導電良好;嚴格控制粉末涂料質量。
七、缺陷名稱:色差
成因分析:粉末顏料不均勻引起色差;不同批次粉末涂料;固化溫度及時間不同;涂層膜厚不均勻。
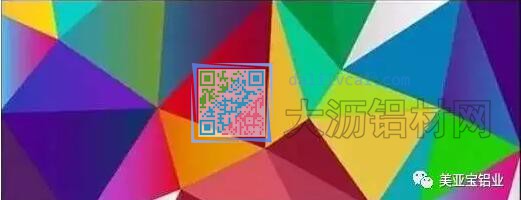
控制措施:加強粉末質量監(jiān)控;不同批次的粉末涂料,新粉入庫烤板檢驗;保持同一批噴涂型材固化溫度和時間一致,特殊粉末須固定生產(chǎn)線涂裝鋁材;加強噴粉工藝控制,避免涂層膜厚差距過大。
八、缺陷名稱:涂層擦劃傷
成因分析:噴涂成品下排、周轉、貼膜前,由于長短料相互摩擦,或人工操作不當,造成噴涂料裝飾面擦劃傷。
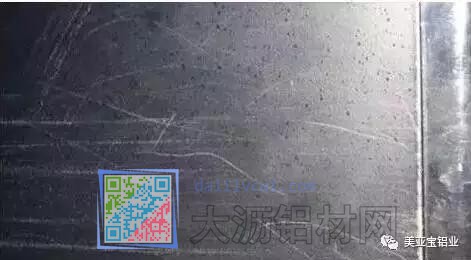
控制措施:將下排的噴涂成品按長度不同,分類放置;工人搬運型材時須相互配合,做到輕拿輕放。
九、缺陷名稱:吐粉
成因分析:粉末受潮結團而致流化效果差,輸粉管中粉末濃度不均勻;流化板被粉末堵塞,供粉裝置流化效果差;粉管、粉泵、文丘管、靜電針、噴槍嘴等配件上附著粉垢或磨損嚴重,導致出粉量不均勻,出現(xiàn)吐粉現(xiàn)象。
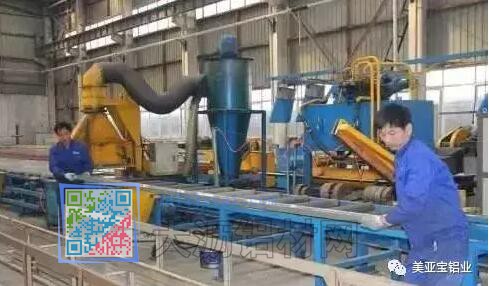
控制措施:改善粉末貯存環(huán)境,粉末使用后及時封箱避免粉末受潮;做好供粉設備維修保養(yǎng);及時清理噴房設備配件上的粉垢,并更換磨損配件。
在實際粉末噴涂生產(chǎn)中,須精細化管理每一道工序,針對出現(xiàn)的涂層缺陷對癥下藥,盡量避免重復出現(xiàn)類似涂層缺陷,這樣才能在降低生產(chǎn)成本的同時提高粉末涂裝質量。