鋁合金和鋼鐵不同,淬火以后的變形鋁合金不能立即強(qiáng)化。它得到的是一種過飽和固溶體組織。這種過飽和固溶體不穩(wěn)定,它有自發(fā)分解的趨勢。在一定的溫度下,保持一定的時間,過飽和固溶體發(fā)生分解(稱為脫溶),引起鋁合金強(qiáng)度和硬度大幅度提高,這種熱處理過程稱之為時效。
在室溫下自然停放一定的時間,鋁合金強(qiáng)度及硬度提高的方法稱為自然時效。入為的將鋁合金制品在高于室溫下的某一溫度,保溫一定的時間,以提高鋁合金強(qiáng)度及硬度的方法稱入工時效。
對于Al-Mg-Si系的6063合金而言,自然時效進(jìn)行得非常緩慢,在室溫下停留半個月,甚至更長的時間,也達(dá)不到最佳的強(qiáng)化效果,比入工時效的強(qiáng)化效果要差30%~50%,所以一般都采用入工時效。含有主要強(qiáng)化相Mg2Si、MgZn和Al2Mg3Zn3的合金、都只有進(jìn)行入工時效才能獲得最高的強(qiáng)度。
含有主要強(qiáng)化相CuAl2和S(A12CuMg)等相的合金,采用自然時效和入工時效兩種方法都可以。如2A11和2A12合金采用自然時效和入工時效都可以獲得最佳強(qiáng)化效果。究竟采用哪種時效方法,這需要根據(jù)合金的本性和用途來決定。一般在高溫下工作的變形鋁合金多采用入工時效,而在室溫下工作的變形鋁合金宜采用自然時效。
二、時效強(qiáng)化機(jī)理
鋁合金的時效強(qiáng)化理論,有很多種說法。如彌散硬化理論、滑移干擾理論、溶質(zhì)原子富集成強(qiáng)化或硬化區(qū)理論等。目前普遍認(rèn)為時效強(qiáng)化或硬化是原子富集形成強(qiáng)化區(qū)的結(jié)果。經(jīng)科學(xué)實(shí)驗(yàn)證實(shí),用X射線方法對鋁合金過飽和固溶體分解動力學(xué)研究和通過電子顯微鏡對薄膜透射觀察,看到中間過渡析出階段(硬化區(qū))的數(shù)量、大小、形狀和分布特點(diǎn),描繪了硬化區(qū)的形象,揭示了鋁合金時效硬化現(xiàn)象的實(shí)質(zhì)。但時效硬化是一個非常復(fù)雜的問題,與合金的成分、時效工藝、生產(chǎn)過程中的加工狀態(tài)都有關(guān)系,目前對時效的認(rèn)識還不十分徹底。下面僅介紹硬化區(qū)理論。
鋁合金在淬火加熱、快速冷卻時,形成過飽和固液體。過飽和固溶體有從不穩(wěn)定狀態(tài)向穩(wěn)定平衡狀態(tài)轉(zhuǎn)變的趨勢。而在過飽和固溶體快速冷卻過程中,合金中的大量空位也被“固定”在晶體中,這些空位的存在加速了溶質(zhì)原子的擴(kuò)散速度,促使溶質(zhì)原子的富集。這些溶質(zhì)原子富集區(qū),開始形成時是無序的,這種無序的富集區(qū)稱GPⅠ分區(qū)。隨著溫度的升高和時間的延長,這些富集起來的溶質(zhì)原子,逐漸有次序的排列起來,這種有序的富集區(qū)稱之GPⅡ區(qū)。
GP區(qū)的大小、數(shù)量決定于淬火溫度和冷卻速度。淬火加熱溫度越高,空位濃度越大,GP區(qū)的數(shù)量增加,GP區(qū)的尺寸減小。冷卻速度越大,固溶體內(nèi)的固定的空位越多,有利于增加GP區(qū)的數(shù)量,減小GP區(qū)的尺寸。當(dāng)時效溫度繼續(xù)升高,或時間延長時,那些大于臨界尺寸的GPⅡ區(qū)發(fā)生長大,形成過渡相θ′(或β′),θ′相的化學(xué)成分與穩(wěn)定相θ(CuAl2)相同,與母體保持有共格關(guān)系,有效阻礙了金屬晶體的變形,因而大大提高了金屬的強(qiáng)度。當(dāng)溫度進(jìn)一步升高或時間進(jìn)一步延長時,過渡相θ′(或β′)變成了θ(CuAl2)相,這時的θ相完全脫離了母相,并有自己獨(dú)立的晶格。這時合金的強(qiáng)度已超過最大值,開始下降,稱為過時效。總之合金的時效過程是過飽和固溶體的分解脫溶過程,具有一定的順序:先形成GPⅠ區(qū),GP區(qū)的有序化形成GPⅡ區(qū),形成過渡相θ′(或β′),最后形成平衡相。
脫溶時為什么不直接形成平衡相?這是由于平衡相一般與基體形成新的非共格界面,界面能大,而亞穩(wěn)定的脫溶產(chǎn)物θ′相與基體完全或部分共格,界面能小。相變初期新相的比表面大,因而界面能起決定作用。界面能小的相,形功小,容易形成。所以首先形成形核功最小的過渡相,再演變成平衡穩(wěn)定相。
不同合金系脫溶序列不一定相同。如Al—Cu系合金可能出現(xiàn)兩種過渡相礦θ〞及θ′而大部分合金只存在一種過渡亞穩(wěn)定相,表3—5—5為幾種合金系的脫溶序列。
表3—5—5主要鋁合金系的脫溶序列
合金系 |
脫溶序列及平衡脫溶相 |
A1—Cu A1—Ag A1—Zn—Mg
Al一MG—Si A1—Cu—Mg |
GP區(qū)(盤狀) →θ″ →θ′ →θ(CuAl2) GP區(qū)(球狀) →g′→g (AlAg2) GP區(qū)(球狀) →h′ →h (MgZn2) ↘ T′→T(A12Mg3Zn3) GP區(qū)(桿狀) →b′→b (MG2Si) GP區(qū)(桿或球狀) →S′ →S(Al2CuMg) |
圖3—5—6表明Al—Cu合金在130℃時效硬度和結(jié)構(gòu)的變化情況。由圖可知:時效各階段順序并不是截然分開的,而是在前一階段尚未結(jié)束時,后一階段則已經(jīng)開始。同時也可以看出時效硬化的主要結(jié)構(gòu)是GPⅠ區(qū)和GPⅡ區(qū),時效硬度最高峰在GPⅡ區(qū)末期和過濾相θ′的初期。當(dāng)大量出現(xiàn)平衡相θ時,軟化明顯,說明過時效發(fā)生。
圖3—5—6 A1—Cu合金在130℃時效硬度及結(jié)構(gòu)變化圖
三、6063合金的入工時效工藝
6063合金的時效工藝比較成熟,一般選擇加熱保溫溫度為170~220℃,保溫l~8h。時效溫度低則保溫時間長,選擇較高的時效溫度,則保溫時間相應(yīng)縮短。對于不同企業(yè)來說,時效爐的加熱方式、爐子的形狀、大小、溫差各不相同。因此選擇最佳的時效工藝,最好通過實(shí)驗(yàn)來確定。例如切取一批6063合金擠壓制品的時效試樣,按溫度不同分成若干組,在每一個溫度下,又分為不同的保溫時間,進(jìn)行時效試驗(yàn)。然后將試樣分別測定抗拉強(qiáng)度,不同溫度、不同保溫時間測得的抗拉強(qiáng)度值列于表3—5—6中。最后將表中數(shù)據(jù)繪成時效硬化曲線。如圖3—5—7所示。
由圖可知:時效溫度為l80℃時,達(dá)到6063合金國家標(biāo)準(zhǔn)的抗拉強(qiáng)度的保溫時間要4 h以上;時效溫度為l90℃時,則需要2.5 h以上;時效溫度為200℃時,則只需要l h就可以了。目前各個企業(yè)多數(shù)采用下面三個不同的時效工藝:
1)時效溫度180±5℃,保溫4~8 h;
2)時效溫度l90±5℃,保溫3~6 h;
3)時效溫度200±5℃,保溫l.5~3 h。
保溫時間的選擇應(yīng)根據(jù)鋁型材的壁厚和裝料的緊密程度來決定。一般壁厚l.2 mm以下時取下限保溫時間,壁厚在5.0 mm以上取上限保溫時間。在其中間的壁厚選擇上、下限保溫時間的適當(dāng)時間。如裝爐量少,裝料稀疏可以選偏下限的保溫時間;裝爐量多,且擺放致密應(yīng)選偏上限的保溫時間。
從表3—5—6和圖3—5—7可知:時效溫度相差10℃,同一保溫時間下制品的強(qiáng)度相差較大,說明鋁合金的時效效果對溫度十分敏感,為保證制品性能的均勻性和穩(wěn)定性,對時效爐的溫差要求較嚴(yán)。一般應(yīng)在±5℃的范圍內(nèi),最好能控制在±3℃。
表3—5—6不同溫度、不同保溫時間試樣的強(qiáng)度值/MPa
時間/h 溫度/℃ |
1 |
1.5 |
2.O |
2.5 |
3.0 |
4.0 |
5.0 |
6.O |
7.0 |
8.0 |
160 170 180 190 200 210 |
146 150 160 163 |
145 151 155 165 168 |
144 148 153 161 171 174 |
147 150 156 164 178 178 |
150 153 159 167 178 177 |
152 156 162 169 177 175 |
154 158 167 172 176
|
156 160 171 178 173
|
159 163 178 180
|
165 168 179 179
|
圖3—5—7時效硬化曲線
四、其他工業(yè)鋁型材的時效工藝
其他工業(yè)鋁材的擠壓鋁合金有一部分是可以自然時效的。根據(jù)不同合金的特點(diǎn),自然時效的時間長短不同。一般自然時效的合金,淬火后在室溫放置四晝夜均可以達(dá)到最大的力學(xué)性能,自然時效效果最明顯是在24 h之內(nèi),通常在48 h之內(nèi)可以基本完成時效強(qiáng)化過程。圖3—5—8和網(wǎng)3—5—9可以看出自然時效時間對力學(xué)性能的影響。
圖3—5—8 2A11合金機(jī)4 mm棒材自然時效
保溫時間對力學(xué)性能的影響
圖3—5—9 2A12合金ф15 mm棒材自然時效
保溫時間對力學(xué)性能的影響
表3—5—7變形鋁合金人工時效工藝
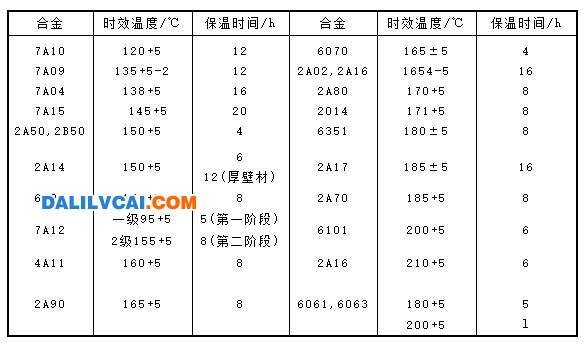
對于可以進(jìn)行自然時效或者人工時效的鋁合金,采用哪種方法時效應(yīng)根據(jù)其使用要求而定。一般來說采用自然時效的鋁合金,屈服強(qiáng)度稍低,而耐蝕性能較好;采用人工時效的鋁合金,其屈服強(qiáng)度較高,而伸長率和耐腐蝕性能降低。但對Al-Zn-Mg-Cu系合金,如7A04合金則相反,采用人工時效時,合金的耐腐蝕性能反而較自然時效的好些。
五、影晌時效效果的因素
1.合金的化學(xué)成分影響
時效強(qiáng)化效果取決于合金組元能否溶于固溶體以及固溶體隨溫度變化產(chǎn)生脫溶相的性質(zhì)和脫溶程度。如錳、硅在鋁中的固溶度較小,且隨溫度變化不大,鎂、鋅雖然在鋁基中有較大的固溶度,但它們與鋁形的化合物的結(jié)構(gòu)與鋁基體的差異較小,強(qiáng)化效果甚微。所以Al-Mn,Al-Si,Al-Mg,Al-Zn系合金通常都不采用時效強(qiáng)化處理。而Al-Cu,Al-Mg-Si和Al-Cu-Mg-Si系合金中的(CuAl2)相、Mg2Si相、S(Al2CuMg)相在高溫下能溶于固溶體中,溶解度隨溫度而變化,因而可以通過淬火、時效提高合金的強(qiáng)度。對于以θ(CuAl2)相、Mg:Si相和S(A12CuMg)相為強(qiáng)化相的合金而言,隨著CuAl2,Mg2Si和Al,CuMg的含量增加,時效強(qiáng)化效果逐漸增加。
2.時效溫度的影響
從圖3—5—7可知,不同時效溫度獲得最大強(qiáng)度值的保溫時間不同或在同一保溫時間下的強(qiáng)度值不同。這是因?yàn)樵诓煌瑴囟葧r效,析出相的臨界晶核大小、數(shù)量、成分以及富集區(qū)長大速度不同。如溫度太低、擴(kuò)散困難,GP區(qū)不易形成或數(shù)量很少,因而時效后的強(qiáng)度低,而時效溫度過高時,擴(kuò)散容易產(chǎn)生,過飽和固溶體析出相粗大,使強(qiáng)度降低,即產(chǎn)生過時效現(xiàn)象。因此每種合金都有在某一保溫時間內(nèi)最佳的時效溫度。不同的時效溫度對時效效果的影響不相同。
應(yīng)當(dāng)指出,一定的時效溫度必須與一定的時效時間相結(jié)合,才能獲得滿意的強(qiáng)化效果。時效時間太短,將使合金時效不充分,降低強(qiáng)化效果。時效時間太長,將會產(chǎn)生過時效,同樣降低強(qiáng)化效果,特別是時效溫度較高時,這種影響更為明顯。
3.淬火到人工時效中間停放時間的影響
從淬火到人工時效中間停放時間,是指擠壓制品經(jīng)風(fēng)冷或水冷到人工時效開始之間的時間,或擠壓制品從淬火爐出來進(jìn)行淬火后到人工時效開始之間的時間。
不同合金的中間停放時間,都會不同程度地影響時效后的強(qiáng)化效果,這種現(xiàn)象稱為“停放效應(yīng)”。對于Al—Mg—Si系合金而言,中間停放時間,根據(jù)其化學(xué)成分的不同,可以使合金的力學(xué)性能降低,也可以使合金的力學(xué)性能提高。如圖3—5—10所示,當(dāng)形成的Mg2Si含量在1.0%以下時,中間停放時間將引起人工時效后強(qiáng)度增加,Mg2Si含量高于l%時,將引起人工時效后強(qiáng)度降低。6063合金的Mg︰Si含量一般在0.8%~l.1%之間,因此室溫停放時間對人工時效后的強(qiáng)度影響不大,甚至還稍有提高。
對于6061合金和硬鋁、超硬鋁合金如7A04,7075等合金,中間停放時間會使人工時效后的強(qiáng)度降低。實(shí)驗(yàn)證明在4~30 h的范圍內(nèi)影響最大。因此這類合金最好在淬火后立即進(jìn)行人工時效。規(guī)定中間停放時間應(yīng)在4 h之內(nèi)。
有人對6A02合金的中間停放時間進(jìn)行研究、對型材抗拉強(qiáng)度的影響如圖3—5—11所示。由圖可知:
1)停放時間很短(1 h以內(nèi)),由于在停放時間內(nèi)自然時效產(chǎn)生的小尺寸GP區(qū),在人工時效溫度下不穩(wěn)定而重新溶于固溶體,形核率降低,人工時效后的型材組織內(nèi)存在粗大過渡相,因而使型材抗拉強(qiáng)度不高。
2)當(dāng)停放時間在2~3 h之內(nèi),可獲得最佳的時效效果。因?yàn)榇藭r獲得了尺寸適當(dāng)?shù)腉P區(qū),它在人工時效開始時穩(wěn)定,形核率高。人工時效時,Mg和Si的原子繼續(xù)向硅偏聚團(tuán)上遷移,大量的穩(wěn)定晶核繼續(xù)成長,形成彌散的Mg2Si強(qiáng)化相,同時CuAl2相也參加時效,型材性能達(dá)到峰值。
3)如果停放時間過長,合金內(nèi)產(chǎn)生大量的大尺寸偏聚團(tuán),使固溶體內(nèi)溶質(zhì)原子濃度降低,人工時效過程中,大于臨界尺寸的GP區(qū)重新溶于固溶體而大量共格析出產(chǎn)物粗大,形成了較大的Mg2Si相粒子,使型材性能降低。
圖3—5—11停放時間對型材抗拉強(qiáng)度影響圖 24 h引起抗拉強(qiáng)度的變化
圖3—5—10 A1-Mg-Si合金淬火后存放
六、分級時效與形變時效
1.分級時效
近年來隨著工業(yè)鋁材的應(yīng)用Et益廣泛,20世紀(jì)70年代研究開發(fā)的一種新的時效方法,分級時效已越來越多被采用。分級時效又稱階段時效。它是把淬火后的制品放在不同溫度下進(jìn)行兩次以上加熱保溫的一種時效方法。在分級時效時,一般都是第一階段采用較低的溫度,促使過飽和固溶體內(nèi)形成大量彌散的GP區(qū)作為向中間相過渡的核心,隨著GP區(qū)密度的增加,也等于加大了中間相的彌散度。第二階段采用較高的溫度時效,促使在較低溫度下形成的GP區(qū)繼續(xù)長大,得到密度較大的中間相,引起制品充分強(qiáng)化。
分級時效與單級時效相比,可以縮短時效時間,并且可以改善超硬鋁合金Al—Zn—Mg和Al—Zn—Mg—Cu系合金的顯微結(jié)構(gòu),可以保持力學(xué)性能不變的情況下,顯著提高合金的耐應(yīng)力腐蝕能力、疲勞強(qiáng)度和斷裂韌度。
分級時效工藝一般都是第一階段溫度較低,要保證形成GP區(qū)在短時間內(nèi)完成。第二階段的時效溫度較高,促使GP區(qū)向中間相轉(zhuǎn)變,以獲得較高的強(qiáng)度和其他良好的性能。幾種超硬鋁合金的分級時效工藝見表3—5—8。
表3—5—8幾種鋁合金的分級時效工藝
3.形變時效
形變時效是把時效硬化和加工硬化結(jié)合起來的一種新的熱處理方法。也稱低溫形變熱處理。通常的處理方式有:
1)淬火——冷變形——人工時效
2)淬火——自然時效——冷變形——人工時效
3)淬火——人工時效(短時)——冷變形——人工時效
形變時效由于把時效硬化與加工硬化結(jié)合起來,增加了合金中的位錯與空位,在固溶體中形成了穩(wěn)定的亞結(jié)構(gòu),因而提高了鋁合金的強(qiáng)度和耐蝕性。
對于不同的合金可以試用不同的低溫形變熱處理工藝組合。低溫形變使合金中形成較多的位錯網(wǎng)絡(luò),使脫溶相形核更廣泛和均勻,利于合金強(qiáng)度提高。合金淬火后,經(jīng)過冷變形再加熱到時效溫度后,脫溶與回復(fù)過程同時發(fā)生,脫溶過程因冷變形而加速,脫溶相質(zhì)點(diǎn)更加彌散。冷變形使合金產(chǎn)生大量的位錯塞積與纏結(jié),有利于溶質(zhì)原子的聚集和強(qiáng)化相的形核和析出,使得時效過程加速。
形變時效由于淬火和人工時效之間要進(jìn)行一次冷變形,對于鋁型材來說是不太適用的,因此主要用于板材、管材和棒材。如2A12合金板材淬火后采用小于30%的冷變形,再人工時效,可以提高抗拉強(qiáng)度,在150℃的溫度下抗拉強(qiáng)度可提高13%~l8%。